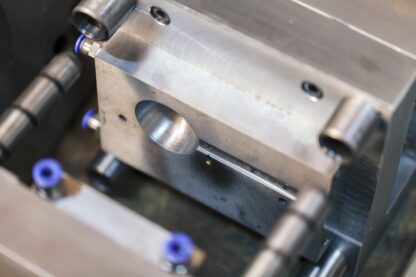
Injection molding prototyping service
Create prototype parts quickly and cost-effectively with precision thermoplastic injection molding.
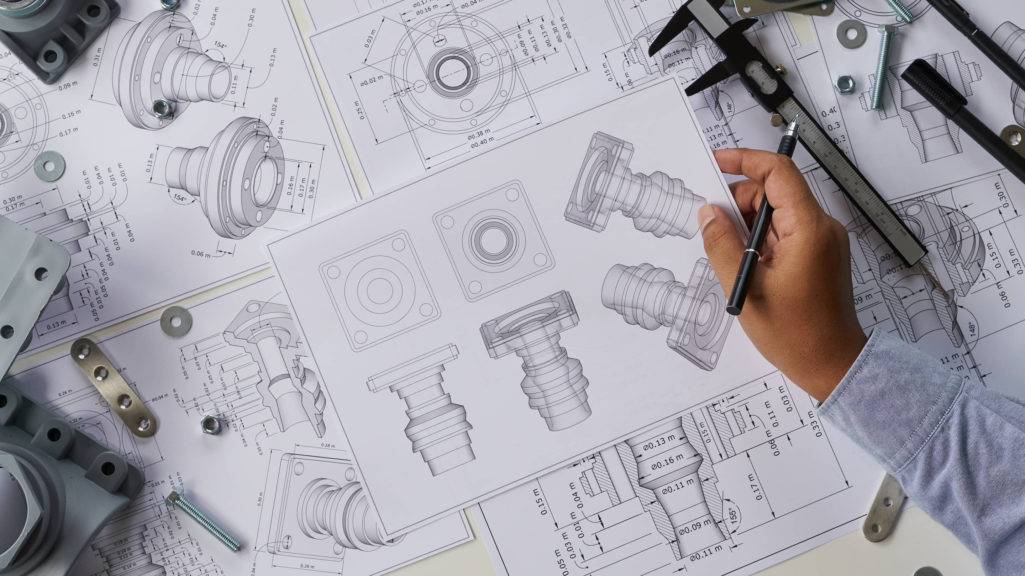
Rapid injection molding prototyping
Our injection molding services, including insert molding and overmolding, enable you to prototype in a range of different thermoplastics, and customize parts with high quality finishes and post-processing options. When you’re ready to move to full production, injection molding prototyping projects can be scaled up quickly.
Creating injection molding prototypes with Fast Radius is simple: upload a CAD file to our Cloud Manufacturing Platform™, work with our engineers to optimize your project, and then move to production when your project is ready.
Learn more about our full range of injection molding services, including multi-cavity molding, insert molding, and overmolding.
Our Injection molding technologies
We offer the following injection molding services:
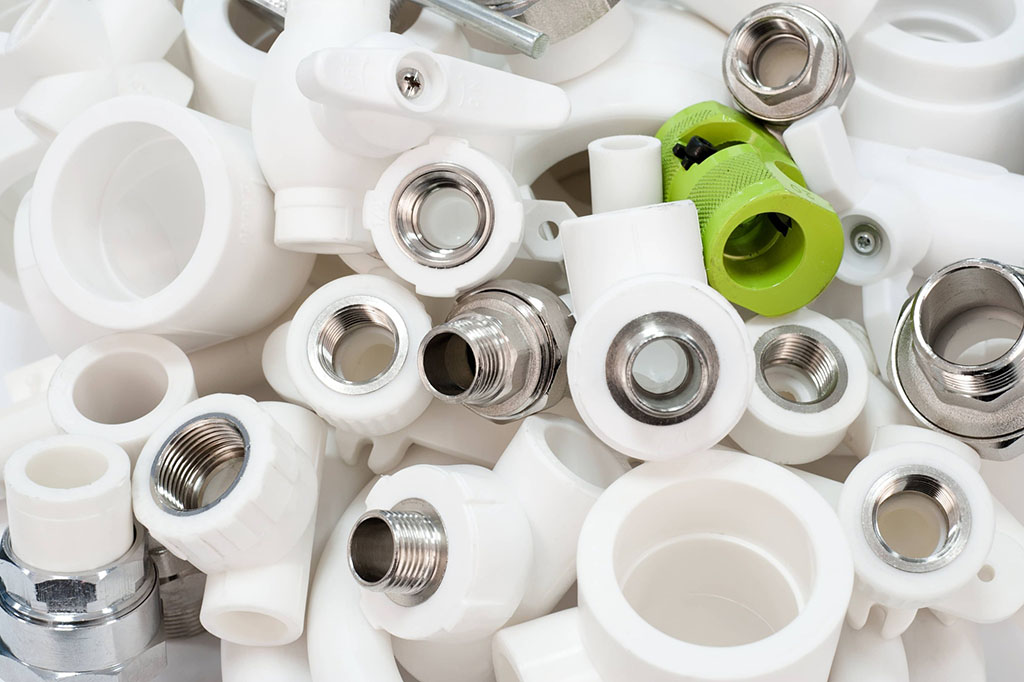
Insert molding
Insert molding involves the injection of molten thermoplastic around a pre-placed insert to create strong, durable prototype parts.

Overmolding
Overmolding is a process in which multiple shots of thermoplastic are injected over or around a substrate to create customized prototype parts.
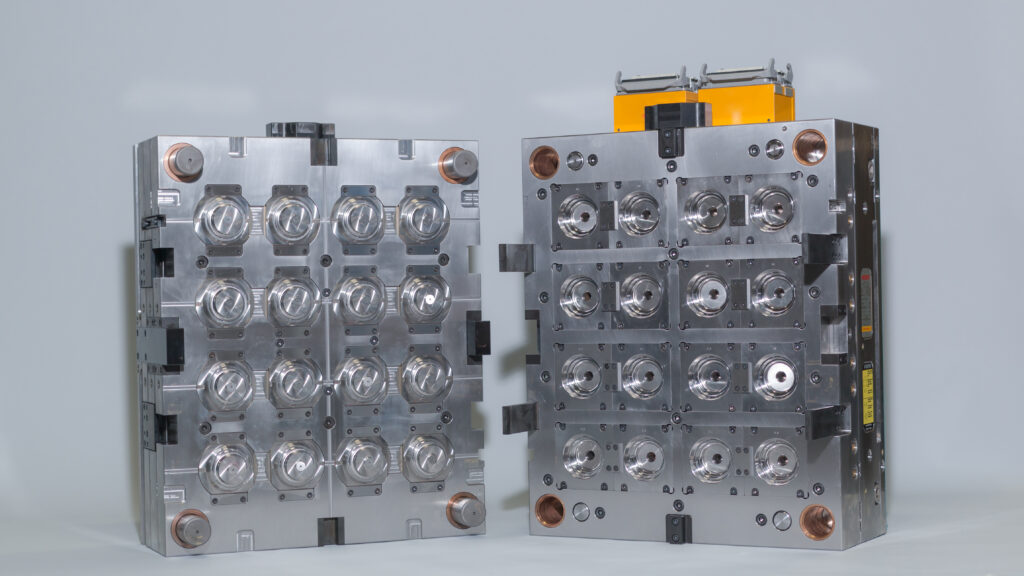
Multi-cavity/family molds
Multi-cavity molds and family molds, enable the production of multiple injection molded parts from a single shot of thermoplastic.
Design considerations
Unlock the potential of your injection molding prototyping project with the following design considerations, production materials, and finishing and post-processing options.
Maximum part size | 800 x 800 x 400 mm 31.5 x 31.5 x 15.7 in |
Minimum part size | 1 x 1 x 1 mm 0.04 x 0.04 x 0.04 in |
Tolerance | Best achievable tolerance: ±0.001″ (0.025mm) Standard: ±0.005″ (0.127mm) For larger part tolerances please contact a Fast Radius engineer |
Lead time | As low as 2 weeks for T1 samples After T1 sample approval, lead time for < 10,000 parts is as low as 1 week |
Tool validation | Standard process is to produce a small set of T1 samples for approval before initiating full production |
Maximum press size | 1600T |
Minimum order size | 100 parts and $5000 |
Set-up fee | $500 per mold per order (applies to sample runs after initial T1 samples or engineering changes) |
Rapid tooling | Molds with steel cavity and core with a shot life of 5,000-10,000 shots Typically machined in 2 weeks |
Production tooling | Steel tool with shot life up to 1M shots Ability to integrate side-pulls or cam-actions Typically machined in 3 weeks |
Multi-cavity or family molds | Multiple identical cavities or family of parts machined into a single tool Allows for more parts to be produced per shot, minimizing unit costs |
Insert molding | Inserts are placed into the mold and molding occurs around them to extend tool life for critical features Allows for inserts such as helicoils to be molded in your design |
Overmolding | Premade parts are placed into the mold and molded over Allows for multi-material injection molding |
Most common materials | Other supported materials | Additives and fiber |
---|---|---|
Acrylonitrile Butadiene Styrene (ABS) | Nylon (PA 6, PA66, PA 12) | UV absorbers |
Polyethylene (PE) | Polycarbonate/Acrylonitrile Butadiene Styrene (PC/ABS) | Flame retardants |
Polypropylene (PP) | Polyurethane (PU) | Plasticizers |
Polycarbonate (PC) | Polymethyl Methacrylate (PMMA/Acrylic) | Colorants |
High Density Polyethylene (HDPE) | Glass fibers | |
Low Density Polyethylene (LDPE) | ||
Polystyrene (PS) | ||
Polyvinyl chloride (PVC) | ||
PEEK | ||
POM (Acetal/Delrin) | ||
Polyethylene Terephthalate (PET) | ||
Thermoplastic Elastomer (TPE) | ||
Thermoplastic Vulcanizate (TPV) | ||
Polyetherimide (PEI) | ||
Polysulfone (PSU) | ||
Inquire for additional options |
Colors | Finishing and post-processing options |
---|---|
Pantone color matching | Standard SPI finishes (A2-D3) |
RAL color matching | Mold-tech textures also available |
Pad printing | |
Inserts (insert molding) | |
Light assembly | |
Protective packaging / film |
Get a quote for your injection molding prototyping project
Create a Fast Radius account for rapid quotes on prototype parts.
Why prototype with injection molding?
The injection molding process offers unique prototyping benefits:
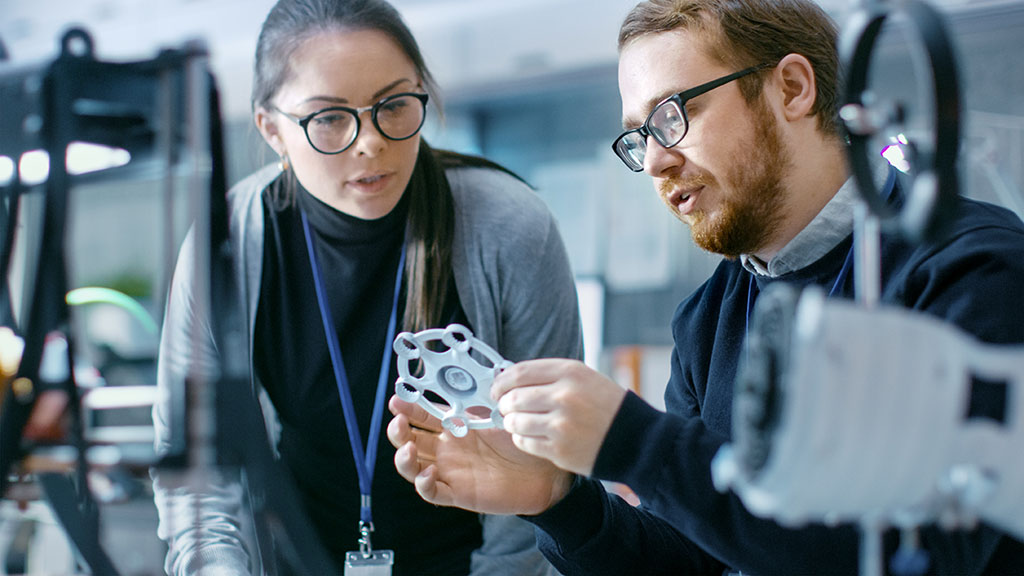
Design freedom
Design prototypes with complete freedom, taking advantage of the full range of Fast Radius insert molding and overmolding capabilities.
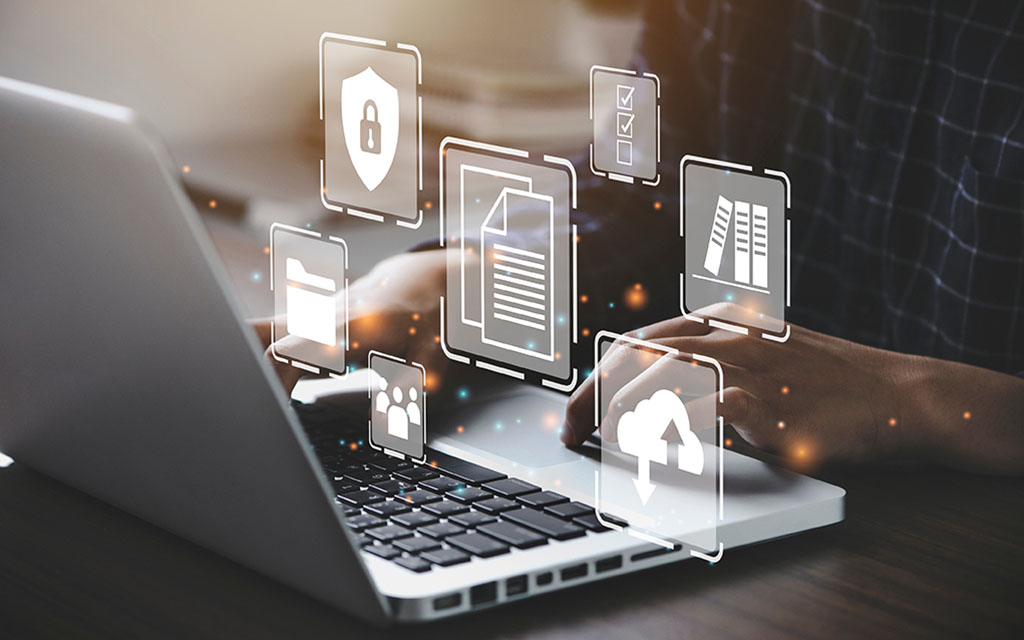
Virtual iteration
Iterate your injection molding prototypes virtually on our Cloud Manufacturing Platform™ and work with Fast Radius engineers to optimize your design.
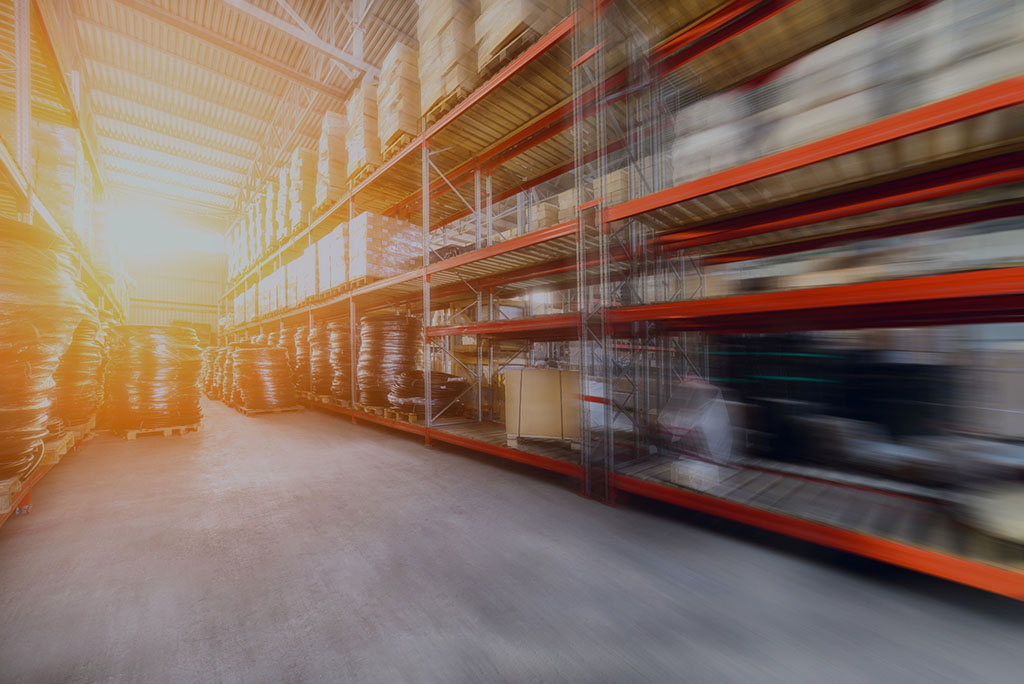
On-demand
Take your prototyping project from design to production quickly and cost-effectively, and manufacture parts on-demand for delivery to your location.
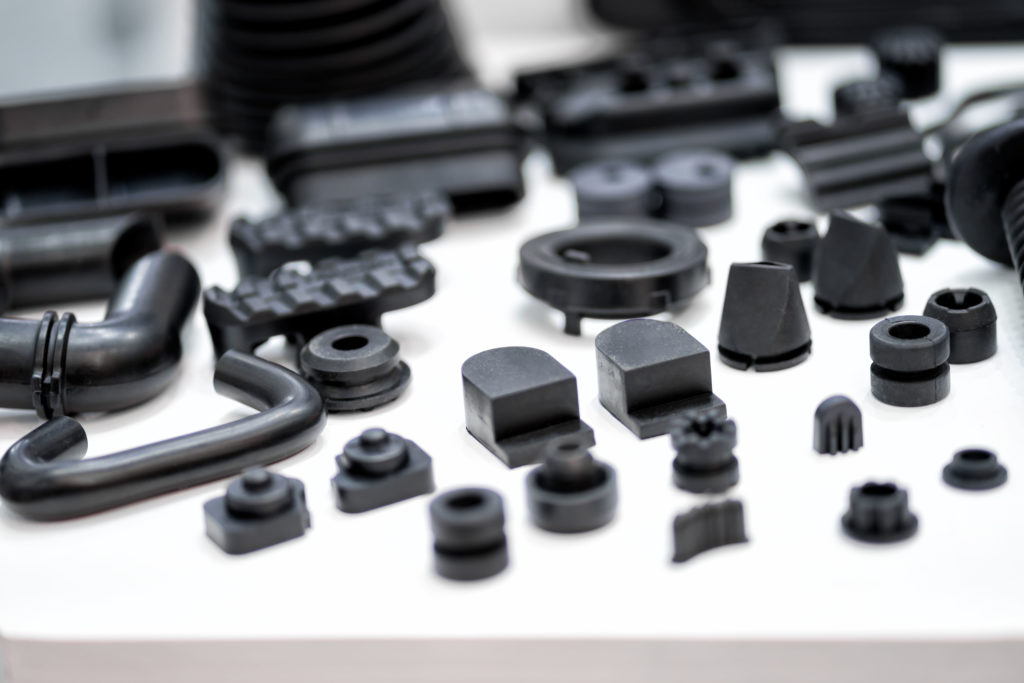
Versatility
Choose from different thermoplastic materials to create your injection molding prototypes, and customize your parts with finishing and post-processing options.
Injection molding applications
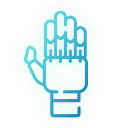
Specialized parts
Injection molding is commonly used to create prototype parts for niche applications, including gaskets, filters, and brackets.
Ergonomic features
Take advantage of an array of customization options to create ergonomic features such as grips, buttons, and knobs, customized for end-uses.
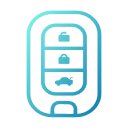
Customer end-use
Design prototypes with high quality, durable features for customer end-use, including scissors, screwdrivers, remote control coverings, and case assemblies.
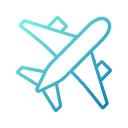
Aerospace and automotive
Injection molded parts can be manufactured to meet precise certification and functionality requirements for use in the aerospace and automotive industries.
Fast Radius manufacturing solutions
Fast Radius manufacturing solutions serve the needs of businesses across the industrial landscape. Explore our capabilities:
3D printing
Fast, scalable, and cost-effective 3D printing technology for a variety of industrial applications.
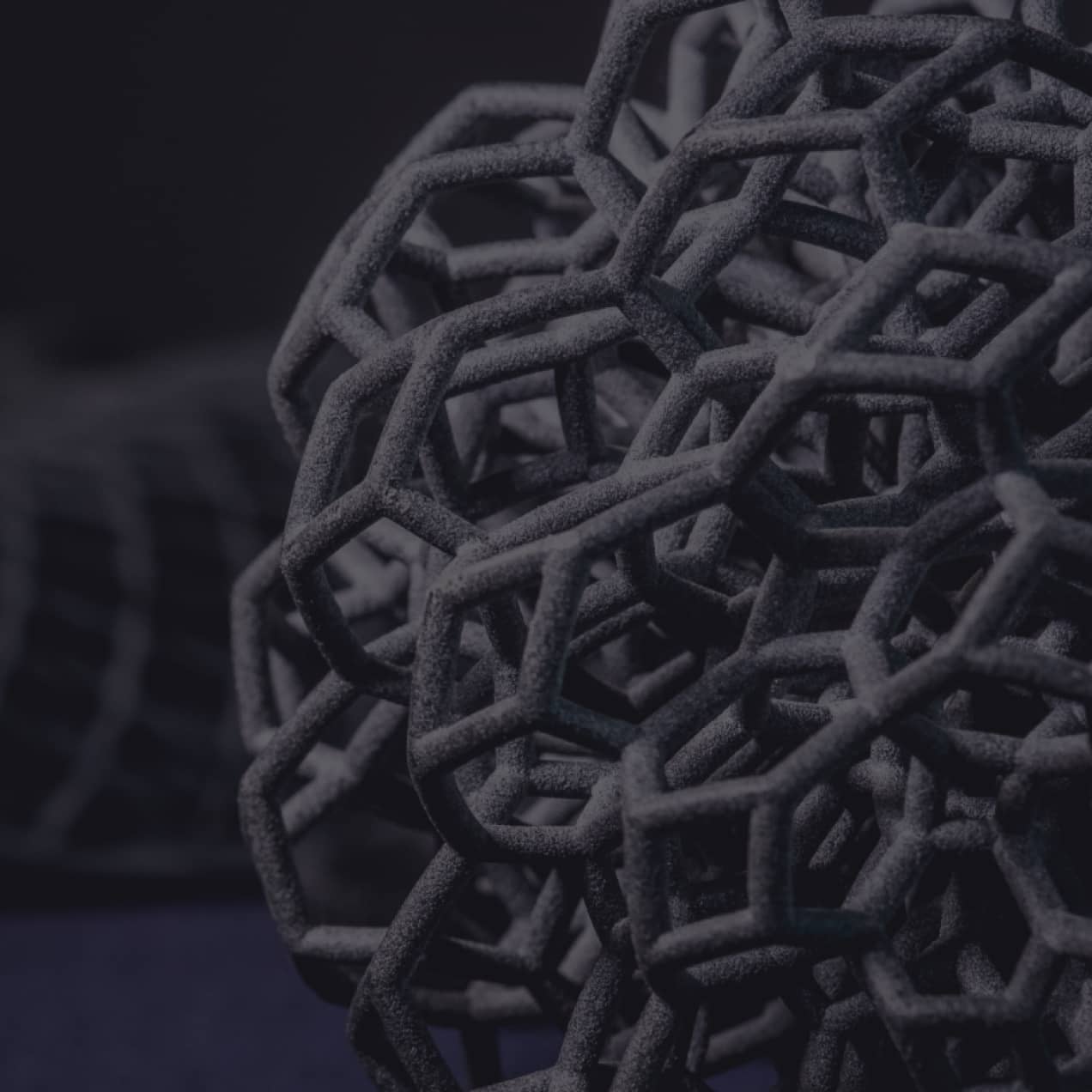
CNC machining
Automated CNC turning and 3-axis and 5-axis milling, using rotating drills, end mills, and lathes.
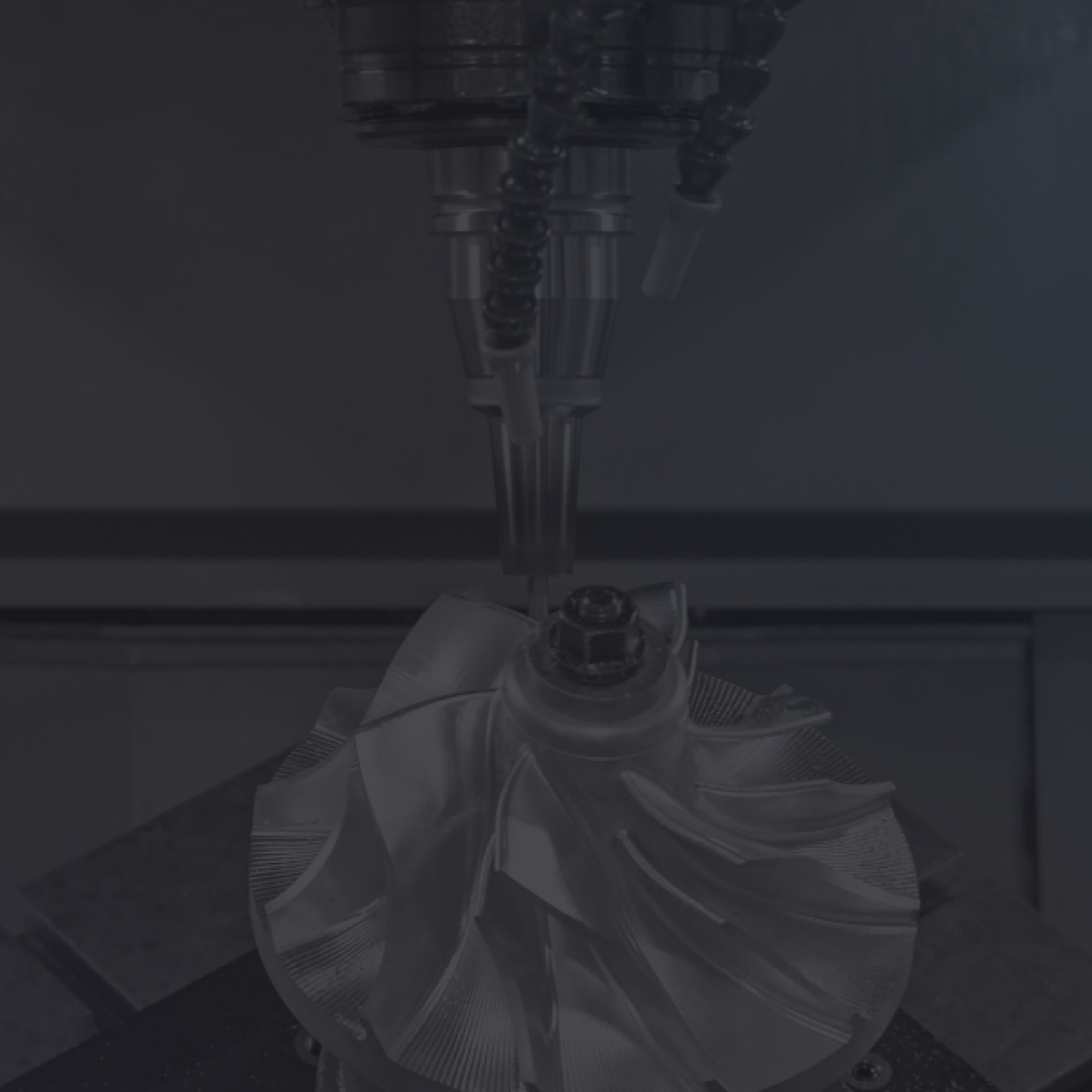