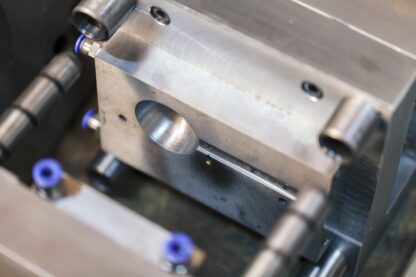
Overmolding service
Manufacture parts with multi-shot thermoplastic injections for enhanced consistency, strength, and durability in high volume projects.
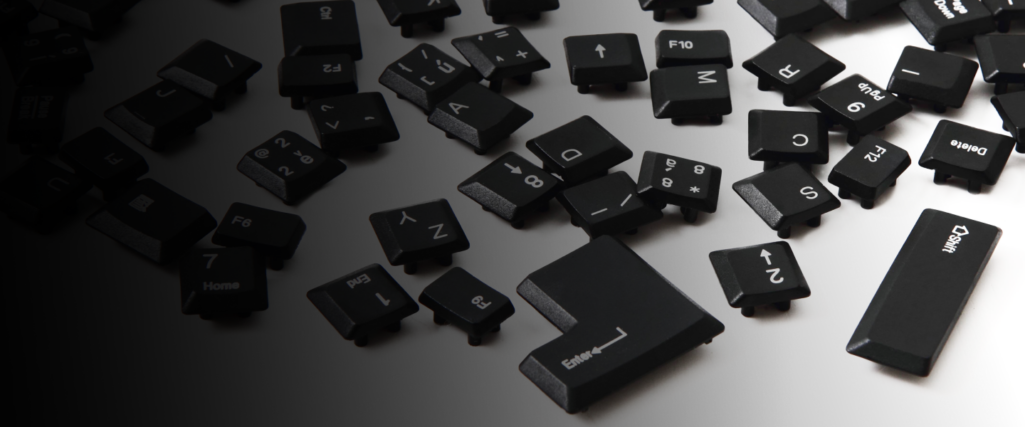
What is overmolding?
Overmolding is an injection molding process in which multiple shots of thermoplastic are injected separately to create a single part. The first thermoplastic injection into a tool or cavity forms a substrate, before an overmolding material is injected into, onto, or around it. The thermoplastic layers bond as they cool to produce a unified and highly durable final product. The bond between substrates depends on the properties of the relevant overmolding materials. Learn more about the bonding process with our material compatibility chart.
Overmolding is ideal for high-volume production runs. Kickstarting your injection molding project is simple. Upload your CAD file to the Fast Radius Cloud Manufacturing Platform™, optimize your design and choose your desired thermoplastic, and then greenlight production with the click of a button.
For more on-demand manufacturing options, browse our injection molding capabilities, including our insert molding and multi-cavity/family molding services.
Design considerations
Unlock the potential of your overmolding project with the following injection molding design considerations, including tooling details, available materials and colors, and finishing and post-processing options.
Substrate wall thickness | The thickness of the substrate’s wall determines how effectively the overmold material flows in, on, and around the substrate. Due to temperature differences between substrate and overmold materials, having an inconsistent wall thickness can lead to warping, increase flash, and render fills incomplete. Ensure that the wall thickness of the substrate and thickness of the overmold are even and consistent from the beginning of the process. Wall thicknesses ranging from 0.060″ to 0.120” (1.5 mm-3 mm) will ensure good bonding in most overmolding applications. |
Maximum part size | 800 x 800 x 400 mm 31.5 x 31.5 x 15.7 in |
Minimum part size | 1 x 1 x 1 mm 0.04 x 0.04 x 0.04 in |
Tolerance | Best achievable tolerance: ±0.001″ (0.025mm) Standard: ±0.005″ (0.127mm) For larger part tolerances please contact a Fast Radius engineer |
Lead time | As low as 2 weeks for T1 samples After T1 sample approval, lead time for < 10,000 parts is as low as 1 week |
Tool validation | Standard process is to produce a small set of T1 samples for approval before initiating full production |
Maximum press size | 1600T |
Minimum order size | 100 parts and $5000 |
Set-up fee | $500 per mold per order (applies to sample runs after initial T1 samples or engineering changes) |
Rapid tooling | Molds with steel cavity and core with a shot life of 5,000-10,000 shots Typically machined in 2 weeks |
Production tooling | Steel tool with shot life up to 1M shots Ability to integrate side-pulls or cam-actions Typically machined in 3 weeks |
Multi-cavity or family molds | Multiple identical cavities or family of parts machined into a single tool Allows for more parts to be produced per shot, minimizing unit costs |
Overmolds | Premade parts are placed into the mold and molded over Allows for multi-material injection molding |
Most common materials | Other supported materials | Additives and fiber |
---|---|---|
Acrylonitrile Butadiene Styrene (ABS) | Nylon (PA 6, PA66, PA 12) | UV absorbers |
Polyethylene (PE) | Polycarbonate/Acrylonitrile Butadiene Styrene (PC/ABS) | Flame retardants |
Polypropylene (PP) | Polyurethane (PU) | Plasticizers |
Polycarbonate (PC) | Polymethyl Methacrylate (PMMA/Acrylic) | Colorants |
High Density Polyethylene (HDPE) | Glass fibers | |
Low Density Polyethylene (LDPE) | ||
Polystyrene (PS) | ||
Polyvinyl chloride (PVC) | ||
PEEK | ||
POM (Acetal/Delrin) | ||
Polyethylene Terephthalate (PET) | ||
Thermoplastic Elastomer (TPE) | ||
Thermoplastic Vulcanizate (TPV) | ||
Polyetherimide (PEI) | ||
Polysulfone (PSU) | ||
Inquire for additional options |
Colors | Finishing and post-processing options |
---|---|
Pantone color matching | Standard SPI finishes (A2-D3) |
RAL color matching | Mold-tech textures also available |
Pad printing | |
Inserts (e.g. heat stake inserts) | |
Light assembly | |
Protective packaging / film |
Get an instant quote for your overmolding project
Use our quoting platform for quick quotes on injection molded parts.
Why choose overmolding?
Overmolding produces strong, long-lasting parts for improved component reliability.
Explore the key benefits and challenges of the process:
Benefits
- Strong, durable parts
- High consistency and precision
- Customization potential
- Cosmetic finishing options
- Create safe, comfortable parts for customer end-use
Challenges
- Requirement to check compatibility between thermoplastic materials
- Precision set-up required to prevent fractures.
- Requires 2 mold cavities to produce the substrate and the overmold
- Upfront design and tooling costs
Overmolding applications
Overmolding is used to produce customized parts and components for a variety of applications:
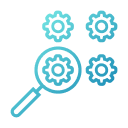
Niche manufacturing
The overmolding process is useful for the manufacture of niche, durable parts, including gaskets, filters, and brackets. Overmolding is also suitable for functional prototyping.
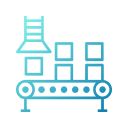
High-volume production
Overmolding produces consistent parts quickly with low tooling costs, and is ideal for projects with high volume production requirements.
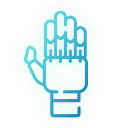
Medical devices
The overmolding process is capable of creating specialized parts with complex dimensions, making it particularly useful for manufacturing medical devices and instruments, and high-end consumer-grade products.
Ergonomic features
Overmolding offers a range of customisation and finishing options, and can be used to add grips, buttons, knobs, and other ergonomic features to pre-existing parts while minimizing additional labour.
Fast Radius manufacturing solutions
Fast Radius manufacturing solutions, including overmolding, are used by businesses across the world. Learn more about our manufacturing capabilities:
3D printing
Fast, scalable, and cost-effective 3D printing technology for a variety of industrial applications.
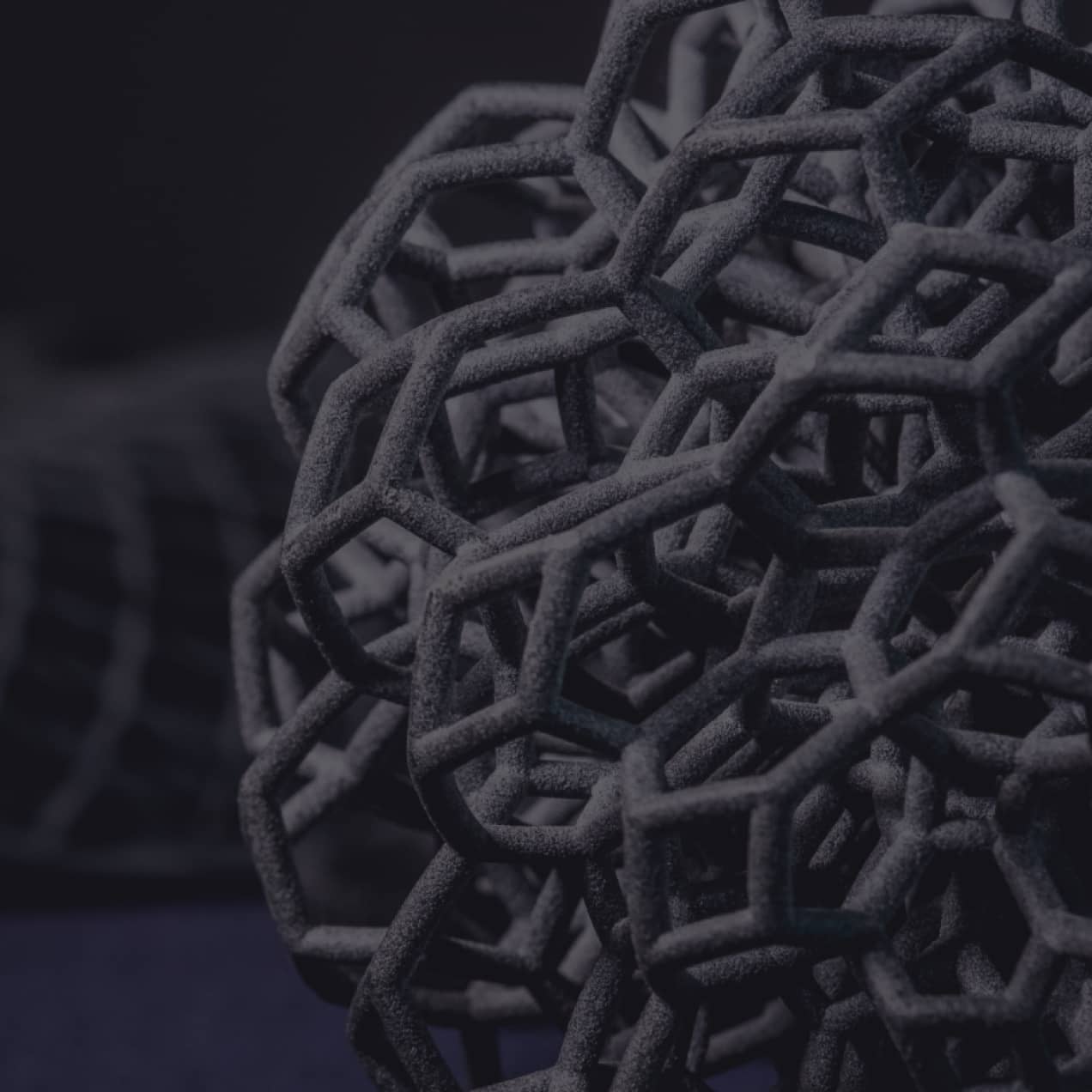
CNC machining
Precision computer-controlled machining processes, utilizing rotating drills, end mills, and lathes.
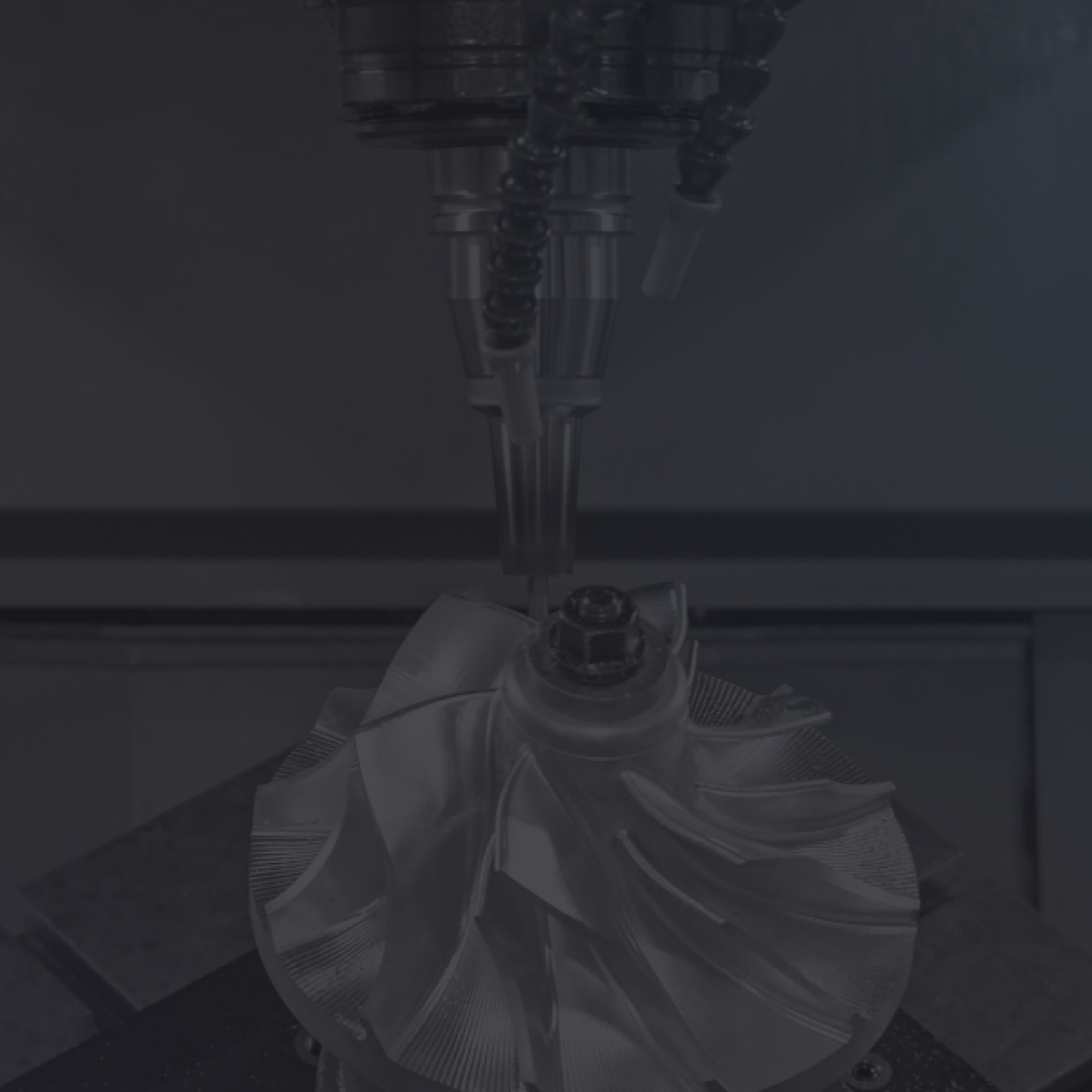