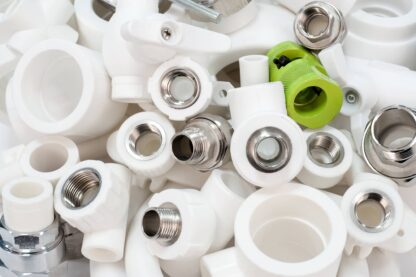
Insert molding service
Create strong, durable parts with thermoplastic injection molding around pre-placed inserts.
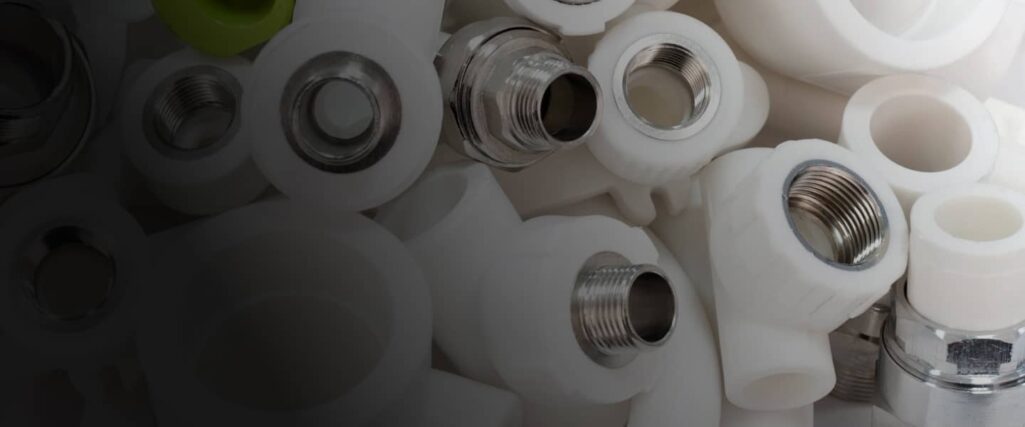
What is insert molding?
Insert molding involves the injection of plastic around a pre-placed insert to shape a strong, durable, and permanent bond between the molded plastic and an insert. During production, an insert is placed inside an empty mold cavity which is then filled with molten thermoplastic and cooled to form a solid part. Cost-effective, precise, and consistent, insert molding is suitable for low to high volume production.
Ordering insert molded parts with Fast Radius is simple. Upload your CAD file to our Cloud Manufacturing Platform™, work with our experts to optimize your design and choose your production material, and then manufacture your products with the click of a button. We also offer heat-staked inserts as a post-processing option for other thermoplastic manufacturing projects.
For more on-demand manufacturing options, browse our injection molding capabilities, including our overmolding services.
Design considerations
Fast Radius injection molding services enable you to manufacture parts to meet a variety of functional needs. Unlock the potential of your insert molding project with the following injection molding design considerations:
Maximum part size | 800 x 800 x 400 mm 31.5 x 31.5 x 15.7 in |
Minimum part size | 1 x 1 x 1 mm 0.04 x 0.04 x 0.04 in |
Tolerance | Best achievable tolerance: ±0.001″ (0.025mm) Standard: ±0.005″ (0.127mm) For larger part tolerances please contact a Fast Radius engineer |
Lead time | As low as 2 weeks for T1 samples After T1 sample approval, lead time for < 10,000 parts is as low as 1 week |
Tool validation | Standard process is to produce a small set of T1 samples for approval before initiating full production |
Maximum press size | 1600T |
Minimum order size | 100 parts and $5000 |
Set-up fee | $500 per mold per order (applies to sample runs after initial T1 samples or engineering changes) |
Rapid tooling | Molds with steel cavity and core with a shot life of 5,000-10,000 shots Typically machined in 2 weeks |
Production tooling | Steel tool with shot life up to 1M shots Ability to integrate side-pulls or cam-actions Typically machined in 3 weeks |
Multi-cavity or family molds | Multiple identical cavities or family of parts machined into a single tool Allows for more parts to be produced per shot, minimizing unit costs |
Inserts | Inserts are placed into the mold and molding occurs around them to extend tool life for critical features Allows for inserts such as helicoils to be molded in your design |
Most common materials | Other supported materials | Additives and fiber |
---|---|---|
Acrylonitrile Butadiene Styrene (ABS) | Nylon (PA 6, PA66, PA12) | UV absorbers |
Polyethylene (PE) | Polycarbonate/Acrylonitrile Butadiene Styrene (PC/ABS) | Flame retardants |
Polypropylene (PP) | Polyurethane (PU) | Plasticizers |
Polycarbonate (PC) | Polymethyl Methacrylate (PMMA/Acrylic) | Colorants |
High Density Polyethylene (HDPE) | Glass fibers | |
Low Density Polyethylene (LDPE) | ||
Polystyrene (PS) | ||
PEEK | ||
POM (Acetal/Delrin) | ||
Polyethylene Terephthalate (PET) | ||
Thermoplastic Elastomer (TPE) | ||
Thermoplastic Vulcanizate (TPV) | ||
Polyetherimide (PEI) | ||
Polysulfone (PSU) | ||
Inquire for additional options |
Metal | Plastic |
---|---|
Brass | Polypropylene (PP) |
Stainless steel | Polyamide (Nylon) |
Aluminum 6061 | Acrylonitrile Butadiene Styrene (ABS) |
Aluminum 7075 |
Injection molding finishing and
post-processing
We can apply a range of injection molding finishing and post-processing options to insert molded parts:
Colors | Finishing and post-processing options |
---|---|
Pantone color matching | Standard SPI finishes (A2-D3) |
RAL color matching | Mold-tech textures also available |
Pad printing | |
Inserts (e.g. heat stake inserts) | |
Light assembly | |
Protective packaging / film |
Get an instant quote for your insert molding project
Use our quoting platform for quick quotes on injection molded parts.
Why choose insert molding?
Versatile and cost-effective, insert molding offers the following key benefits and challenges:
Benefits
- Precision production at low or high volume
- High quality, permanent bonds
- Strong, durable final products with reduced assembly and labor costs
- Multi material production possibilities
- Different inserts offer different mechanical qualities and functions
Challenges
- Requirement to use suitable resins to prevent plastic cracking around insert
- Slight increase in molding costs due to increased cycle time required for each part to add the inserts
Insert molding applications
From functional prototypes to full production runs, insert molding’s key industrial applications include:
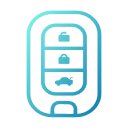
Consumer-facing products
Insert molded parts can be created from a variety of high quality materials with finishing options that are ideal for consumer-facing products.
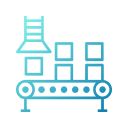
Low volume production
Insert molding offers consistency and cost-effectiveness and is an ideal process for low-volume manufacturing projects.
Handheld devices
Insert molding is used widely in the production of handheld devices, such as scissors, screwdrivers, remote control coverings, case assemblies, knobs, and dials. Insert molding is also used in the manufacture of medical implants.
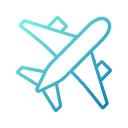
Aerospace and automotive
Strong and durable, insert molded parts are used in a variety of aerospace and automotive contexts, where they are manufactured to meet precise industry standards and certification requirements.
Fast Radius manufacturing solutions
Fast Radius manufacturing solutions, including insert molding, are used by businesses across the world. Learn more about our manufacturing capabilities:
3D printing
Fast, scalable, and cost-effective 3D printing technology for a variety of industrial applications.
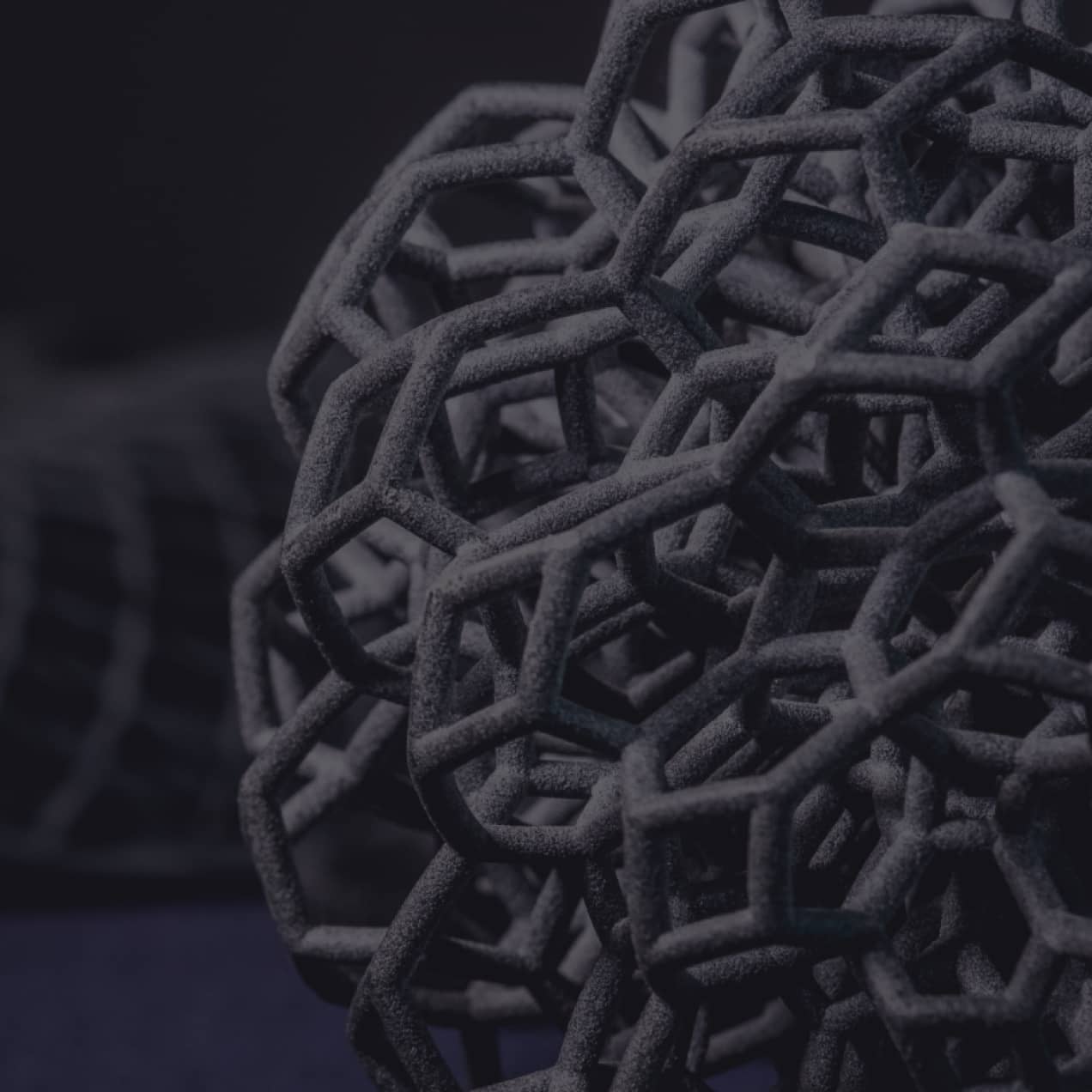
CNC machining
Automated CNC turning and 3-axis and 5-axis milling, using rotating drills, end mills, and lathes.
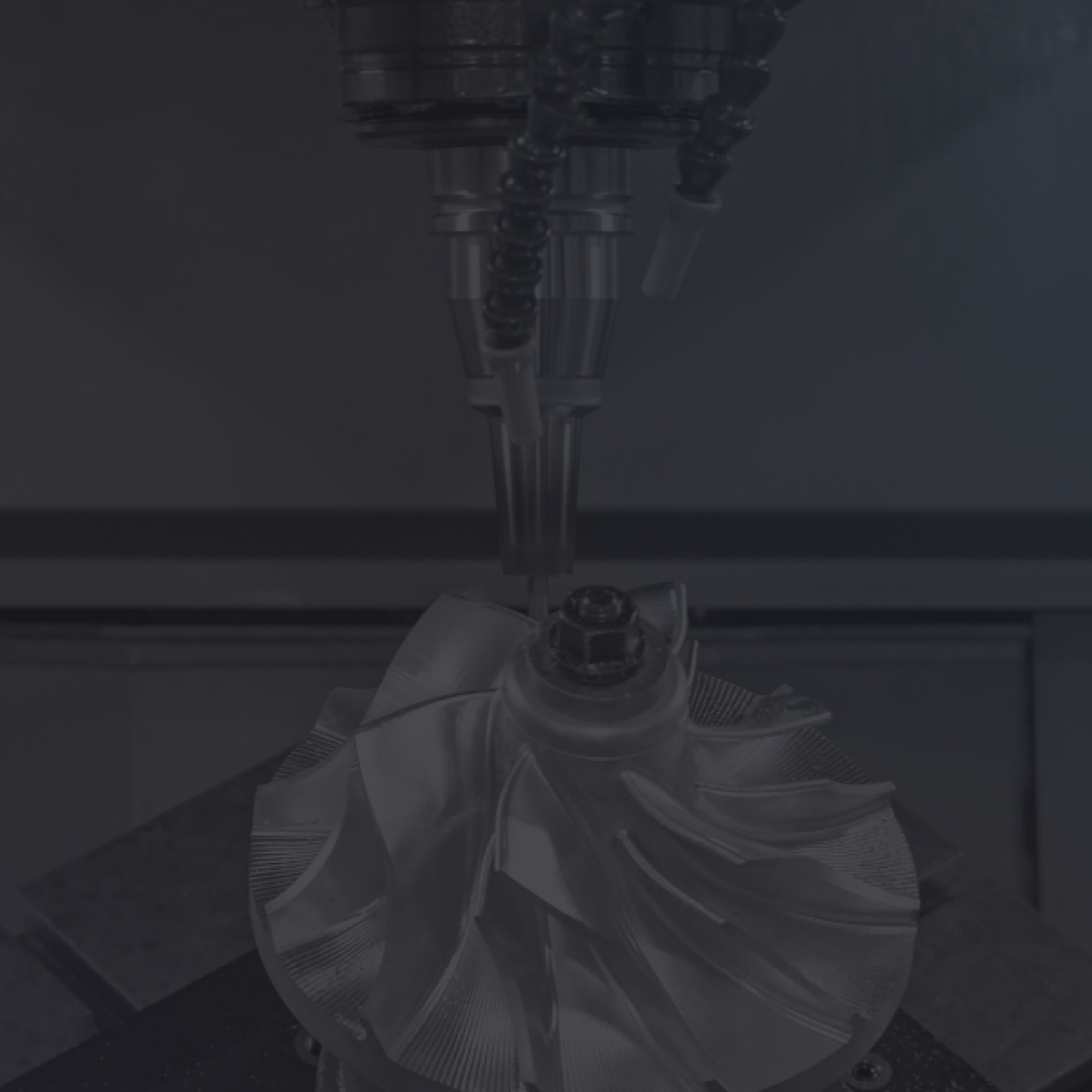