Making faster factories possible
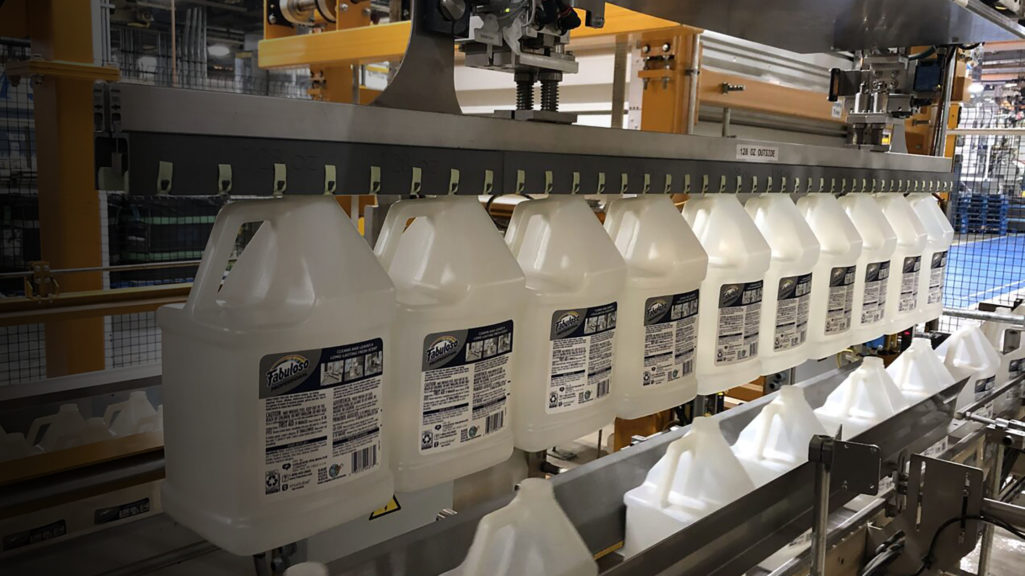
Colgate needed to improve efficiency on a bottling line where a malfunctioning part was causing stoppages and waste. Fast Radius working closely with Colgate’s engineers designed a solution that relied on two additive technologies, resulting in reduced unplanned downtime and greater production throughput.
THE CHALLENGE
Reducing downtime on a busy factory line
In order to keep production running at full capacity, Colgate needed an inventive fix for an ineffective piece of machinery.
Colgate had a bottle accumulator that was not running efficiently. Unexpected failures occurred with a rigid plastic part that was meant to hook a very small ridge on each bottle, lift the bottles, and move them onto the line. The tool frequently missed the ridge, dropping bottles onto the factory floor.
Without a functional bottle accumulator, bottles would accumulate and back up the line, which led to frequent stops and starts that resulted in costly downtime. To tackle this problem, Colgate came to the Fast Radius design engineering team for help designing and producing better tooling that would work with their existing bottle accumulator. By using additive manufacturing, they were able to get the machine back in service quickly.
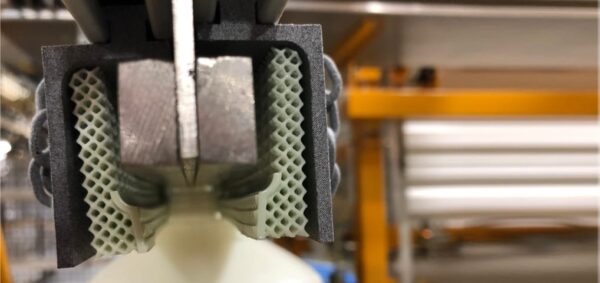
Before we did this work with Fast Radius, the utilization of our bottle accumulator was near zero. With the new gripper designs, the machine is now set to run 100% of the time.

MAKING IT POSSIBLE
Flexible materials and real-world testing
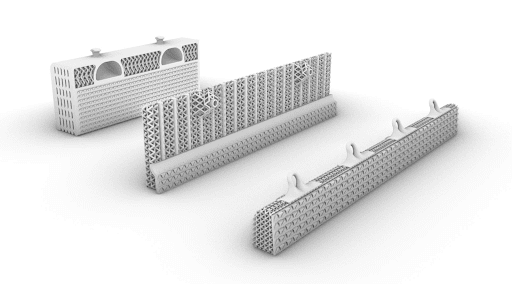
1. Design for additive manufacturing (DfAM)
Fast Radius designed the gripper in two parts, each made with a different additive process. Printed in durable PA 12 using HP MJF technology, the outer portion of the part slides into the metal bottling conveyor and supports the weight of the bottles. The inner portion of the tool is a flexible lattice mesh printed with Carbon’s highly resilient elastomeric polyurethane material, EPU 41,using the Carbon Digital Light Synthesis™ (Carbon DLS™) process. Fast Radius engineers designed a lattice structure that easily conformed to different shapes, meaning it could get a strong grip on bottles of various sizes. While the previous tool needed to be changed out every time Colgate switched between bottle types, the new gripper can be used to pick multiple bottle sizes.
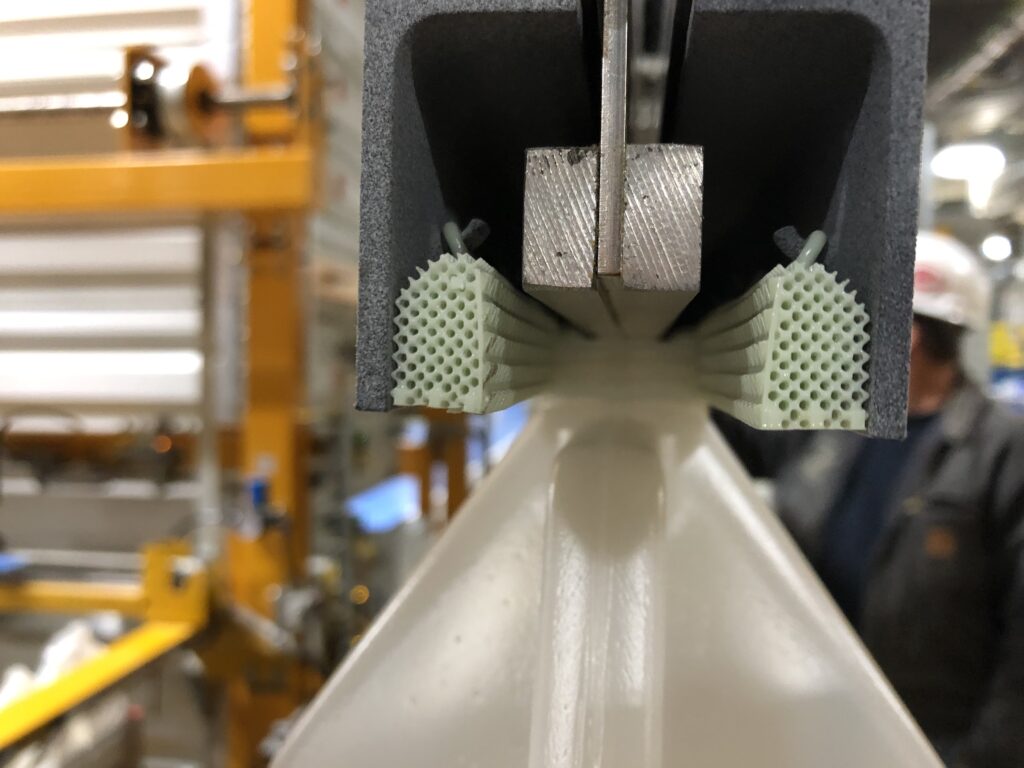
2. High-performance materials
In an industrial setting, it’s crucial to be able to change parts quickly with as few tools as possible for maximum efficiency and minimal downtime. To accomplish this, Fast Radius and Colgate took advantage of the material properties of PA 12 and EPU 41 to design a two-component part that assembles without any fasteners. The EPU 41 inner portion of the bottle gripper seamlessly wraps around and hooks into the strong PA 12 outer portion for a secure assembly. Together the two materials provide the flexibility and strength required to pick up and move bottles without dropping them.
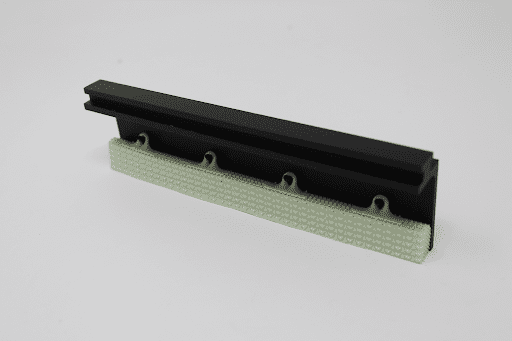
3. Multi-process manufacturing
Fast Radius offers multiple manufacturing technologies under one roof, so they were able to make and assemble Colgate’s parts easily, even though the parts required different processes. Colgate didn’t have to worry about coordinating different suppliers, and they didn’t have to invest in their own additive manufacturing equipment. Beyond access to Fast Radius’ Carbon DLS and HP MJF factories, Colgate was able to work with Fast Radius engineers who are experts in DfAM and identifying the right process for each project.
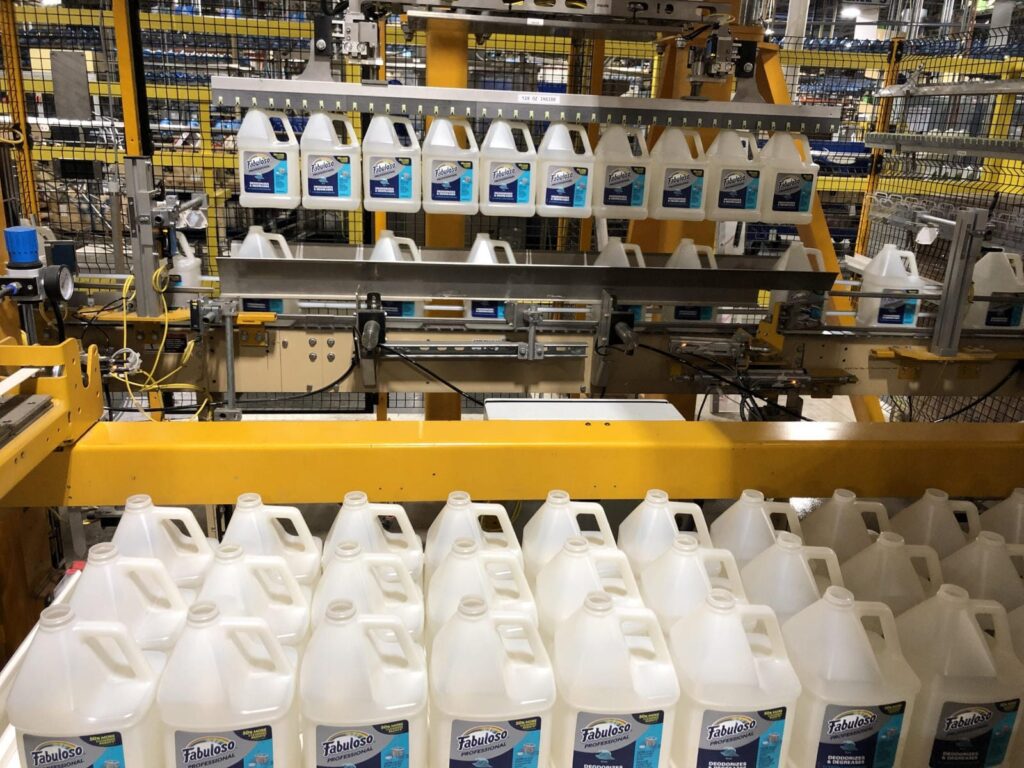
4. Testing in a production environment
Fast Radius and Colgate went through three design iterations to perfect the bottle gripper. Because additive manufacturing allows you to prototype using the same equipment and materials that will be used in the final parts, Colgate was able to test each prototype directly on the bottling line in real working conditions. These tests provided invaluable insight into the performance of the part and made it easy to identify the adjustments needed. Once Colgate accepted the design, the parts were produced immediately and put to work on the line.
The Results
A small part that made a big difference
100%
production capacity
Flexible
Bottle handling
Restored
Operator confidence in machine
Gallery
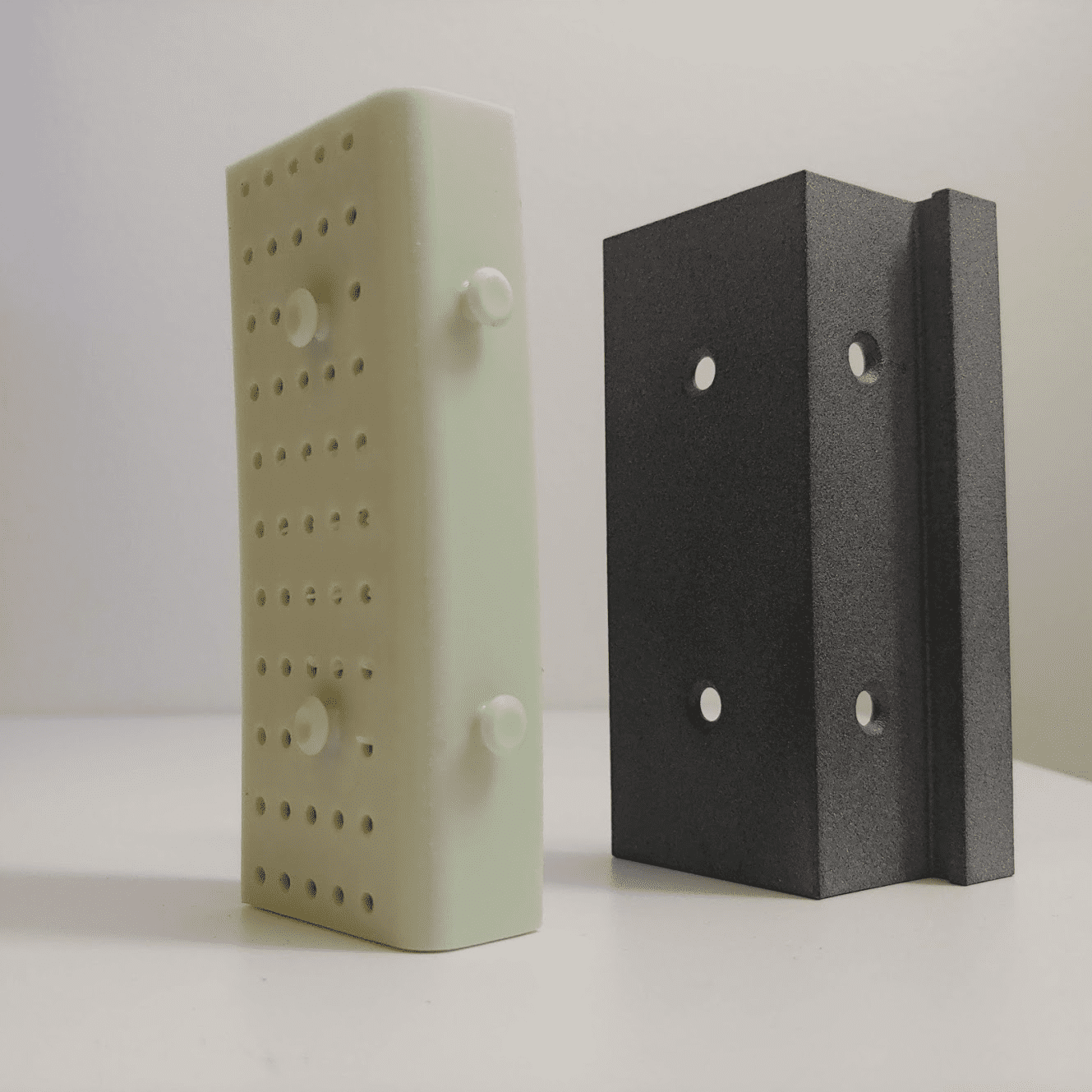
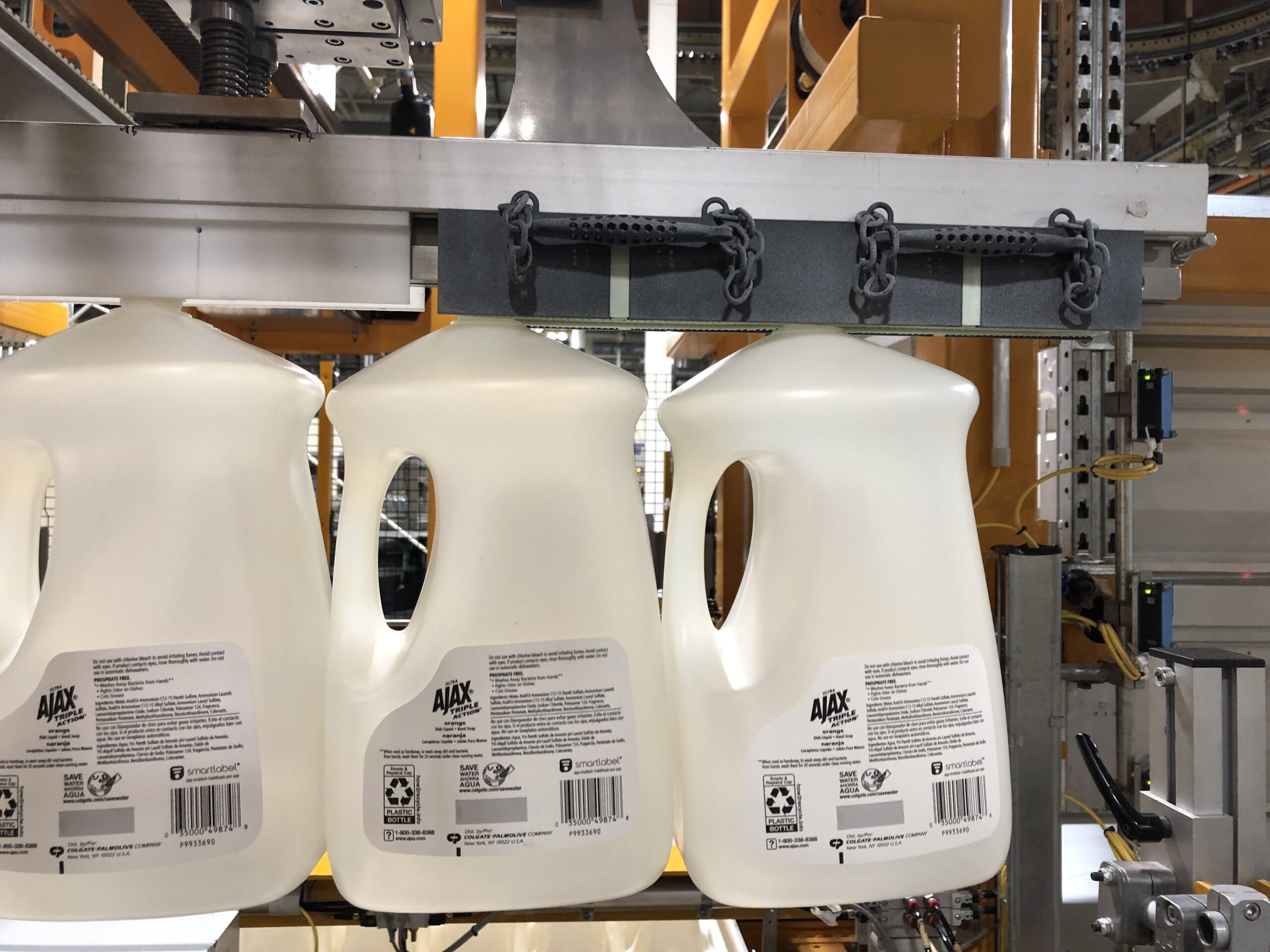