Making controlled movement possible
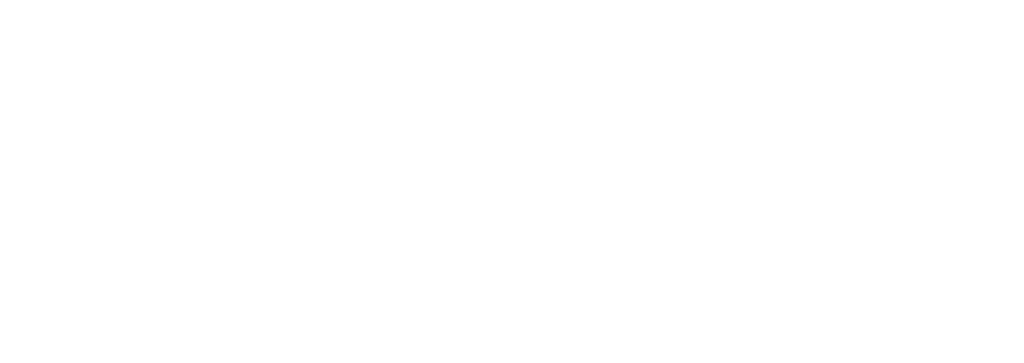
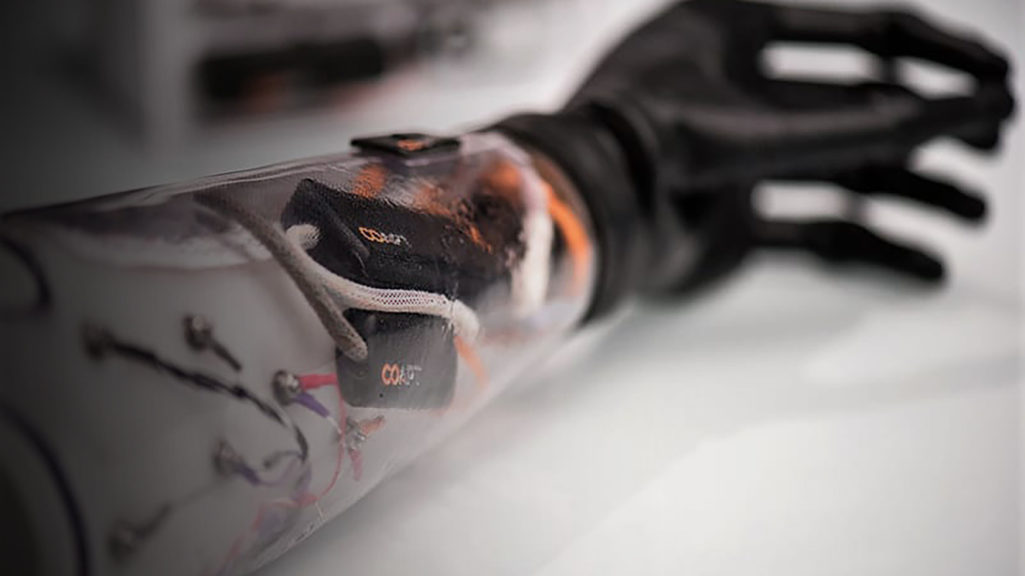
Coapt needed help bringing its next-generation prosthetic arm to life under a tight deadline. Fast Radius optimized 36 unique part designs for efficient additive manufacturing.
THE CHALLENGE
Producing the next generation of prosthesis components in record time
Coapt wanted to make movement second nature with a completely redesigned, innovative medical device.
Coapt is a Chicago-based company that produces myoelectric pattern recognition systems for upper limb prostheses. The Coapt COMPLETE CONTROL system enables people who have lost their upper limbs to fully control movement in their prosthetic arms. It does so through an electrical pattern recognition system that captures coordinated muscle signals sent through the brain, decodes the patterns in real time and translates them into the wearer’s intended movement – such as picking up an object or waving a hand.
In 2018, Coapt gathered enough optimization feedback to begin production on the second generation of COMPLETE CONTROL. This meant retooling the system’s software and redesigning the hardware components. Fast Radius’s innovative manufacturing processes could design and deliver the product in record time.
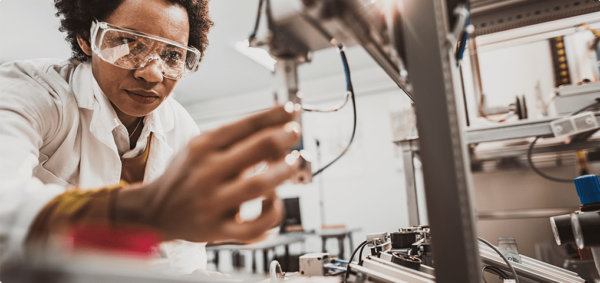
Fast Radius helped us understand all of the additive technologies and materials that were available to us for this project. They guided us in the right direction based on our requirements and were able to give us feedback on how to improve our designs for 3D printing.
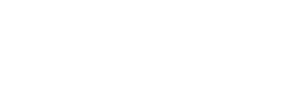
MAKING IT POSSIBLE
Rapid prototyping and development
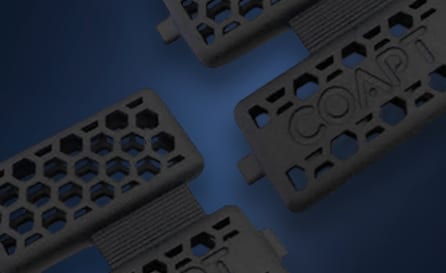
1. Redesign for additive
There were many parts that Coapt wanted to test and make differently in the next wave of COMPLETE CONTROL. And it wasn’t just the geometries that Coapt wanted to iterate, it was also the textures and aesthetics of the parts. With so many variables to consider, injection molding just didn’t make sense — Coapt needed a partner like Fast Radius to redesign several parts of COMPLETE CONTROL. Luckily, Fast Radius provides expert engineering to support additive processes, specifically Carbon® Digital Light Synthesis (DLS) and HP Multi Jet Fusion (MJF).
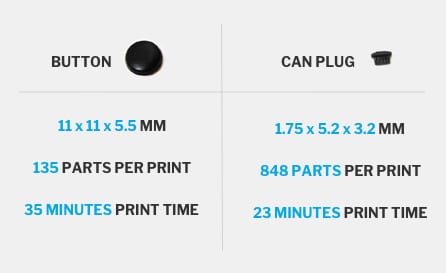
2. Creating small parts at scale
Nearly a dozen core components make up the second generation of COMPLETE CONTROL, each manufactured using the most efficient process for that part. Two of those parts are the calibration button and can plugs. Because of their size and aesthetic requirements, both are manufactured using Carbon® DLS technology and EPU 40 material.
3. Meeting low volume production needs
Coapt chose to make one more critical part using additive manufacturing: The fabrication dummy, a part that the prosthetist uses to ensure that the electronic circuit board housing fits correctly within the wearer’s prosthetic. This part is made using PA 12 material with HP MJF technology – a perfect fit based on the part’s need for rigidity and light weight.
4. Rapid iteration
Over 12 weeks, Fast Radius printed 36 unique designs yielding 195 parts for the Coapt team to test and evaluate. Instead of investing in on-site 3D printing technology for prototyping, Coapt tapped into Fast Radius’s technology infrastructure to make rapid iterations as needed.
THE RESULTS
A strategic manufacturing partnership – from design optimization, to prototyping, all the way to production
195
parts manufactured and evaluated
36
unique designs printed in 12 weeks
983
parts per printed in 58 minutes using Carbon®Digital Light Synthesis®
Gallery
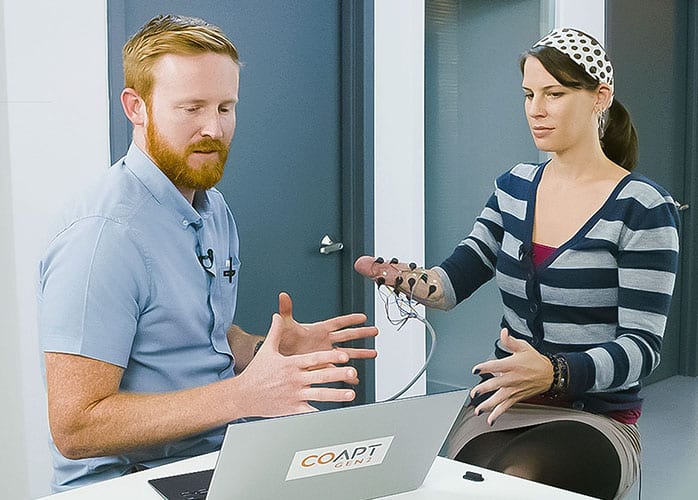
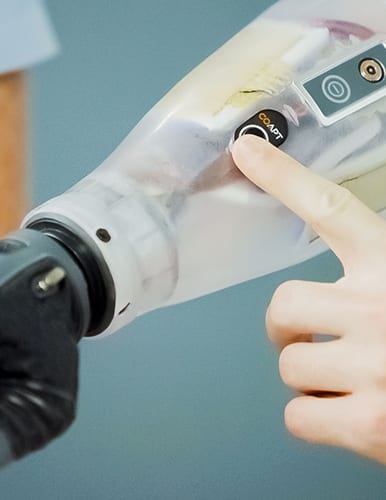