Making cosmetically designed robots possible
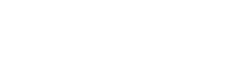
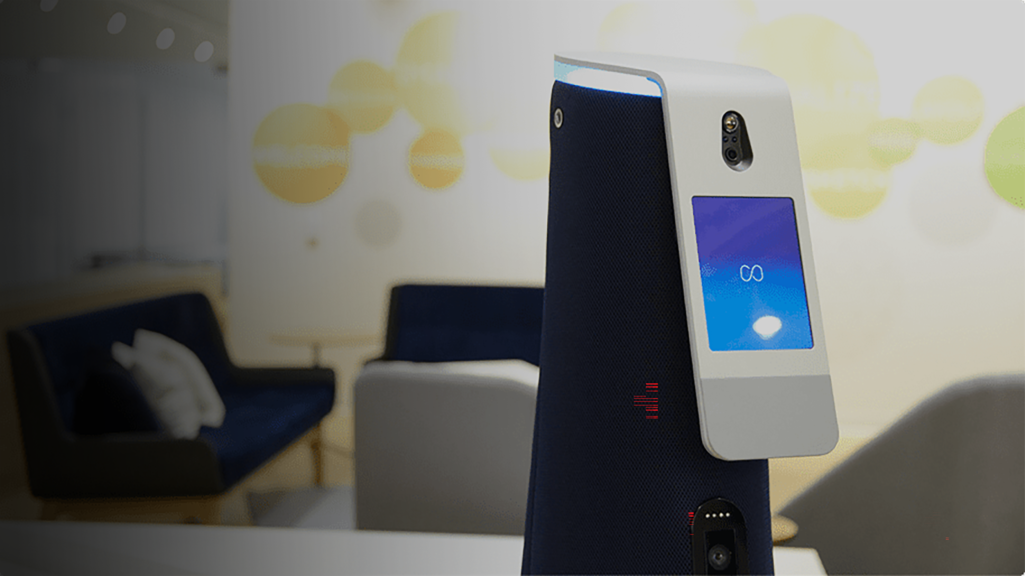
Cobalt Robotics wanted to make their security robots more approachable. Fast Radius met their strict specifications and reduced their urethane casting costs by 60%.
THE CHALLENGE
Making humans comfortable working with robots
Cobalt Robotics wanted to make approachable security robots using thoughtfully manufactured cosmetic components.
Cobalt Robotics produces security robots that make spaces safer, more secure and more productive. But, according to Alejandro Ramirez, Lead Mechanical Engineer at Cobalt, the company’s true end product is much more than that.
“Our mission is to make robots that are useful to society,” said Ramirez. “Our goal is to move toward a harmonious relationship between machines and humans.”
Cobalt’s robots are purposefully designed to not appear humanoid. But because the robot operates in spaces where humans work and live, it was important that the machine still exude an approachability and warmth that would make people feel comfortable interacting with it. That means special attention had to be paid to the cosmetic components of the machine. It was important to Cobalt that the cosmetic plating was made exactly to their design specifications, so they partnered with Fast Radius to manufacture these critical parts.
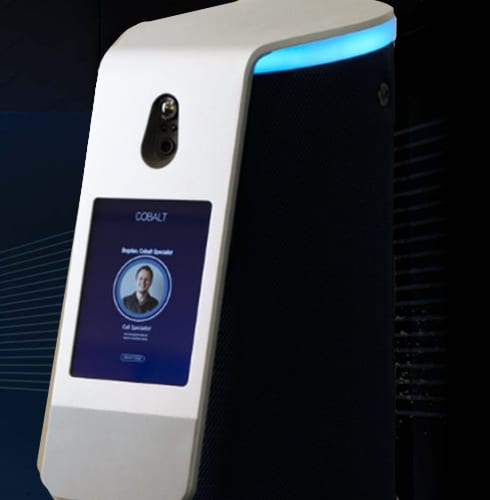
Fast Radius reduced our cost to manufacture urethane parts by 62%, painting and finishing by 90% and 3D printing by 33%.
MAKING IT POSSIBLE
Reducing costs and managing project logistics
1. Advanced manufacturing expertise
The robotics industry moves at an incredibly fast pace. Design decisions and rapid iterations are constantly at play. Fast Radius met Cobalt’s need for speed and agility by providing fast response times, ongoing communication and advanced manufacturing expertise across different processes — which was handy when it came to fixing production errors.
2. True manufacturing partnership
Prior to working with Fast Radius, Cobalt struggled to find a cost-effective supplier that could deliver on the exact specifications of the product. Furthermore, most suppliers were just order takers and didn’t work with Cobalt’s team to find production improvements. Fast Radius advised that new CNC master patterns would be more accurate than Cobalt’s original FDM ones. This discovery resolved previous fitment issues and the team was able to come up with a better, more cost-effective way of producing cast urethane molds for the parts. The changes saved Cobalt 60% on urethane casting production.
3. A commitment to quality
The cosmetic plating was critical to creating a seamless look that would be inviting to the people interacting with the robots. Because of this, the quality considerations were twofold: The parts had to be strong and reliable, and they had to meet high aesthetic standards. From the start, Fast Radius recognized how important quality was to Cobalt, so the team was willing to go through multiple rounds of sample production and feedback in order to get the job done right.
4. Exceeding quality requirements
Part of Fast Radius’s collaboration with Cobalt involved manufacturing plastic mounts meant to house directional technology and three-dimensional depth sensors. By ensuring the precision, quality and accuracy of these manufactured parts, Fast Radius enabled Cobalt’s robots to safely navigate dynamic human environments, encouraging positive human-machine interaction – part of Cobalt’s core mission. In the end, Cobalt reported that Fast Radius consistently met or exceeded Cobalt’s quality requirement of a 95% component yield.
5. Logistics made easier
One of the biggest benefits of working with Fast Radius is the true end-to-end service provided. Fast Radius was helpful in troubleshooting manufacturing issues as well as managing the logistics of the project. Parts were shipped quickly and easily across the globe thanks to Fast Radius’s partnership with UPS.
“Having the Fast Radius team manage all of the logistics was a huge help to my team,” said Ramirez. “We saved about two weeks in overall project time per part produced by allowing Fast Radius to handle those facets of the project, allowing my team to focus on technical aspects.”
THE RESULTS
A cost-saving manufacturing partnership that delivered quality robotics parts and seamless logistics
7%
overall cost reduction
2 weeks
cut off overall project time
62%
urethane manufacturing cost reduction
90%
painting and finishing cost reduction
33%
3D printing cost reduction
Gallery
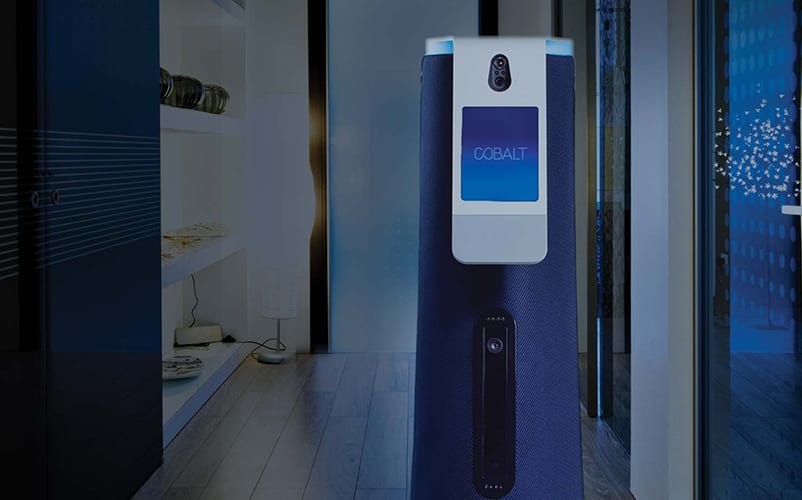
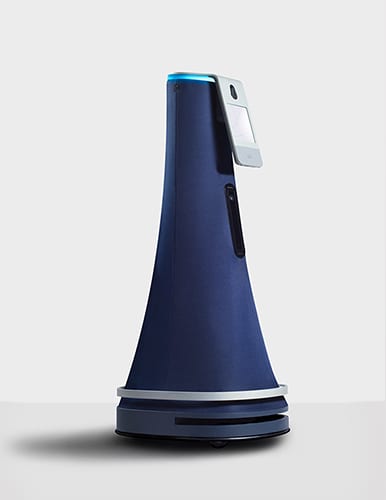
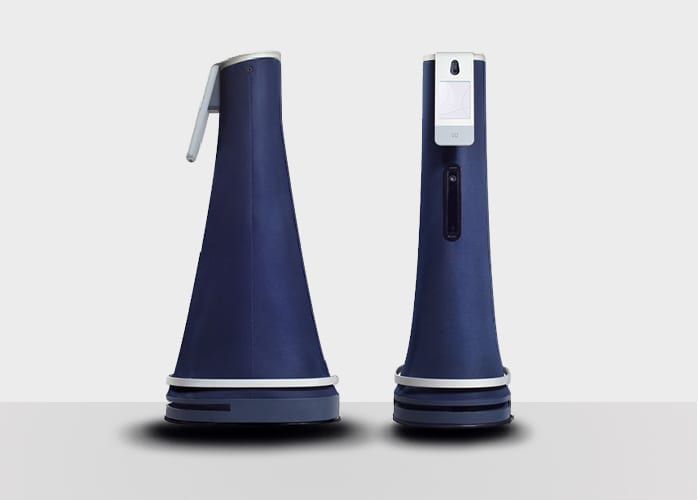
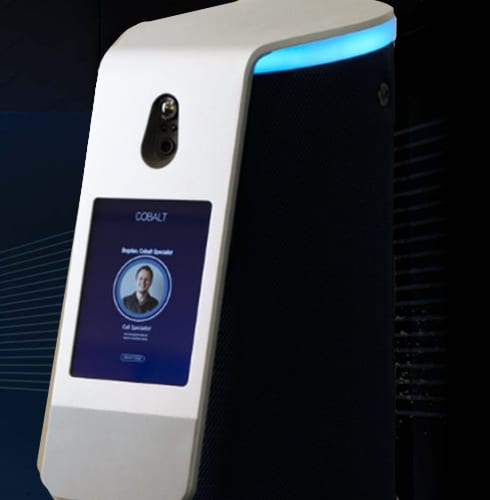