Making faster automotive innovation possible

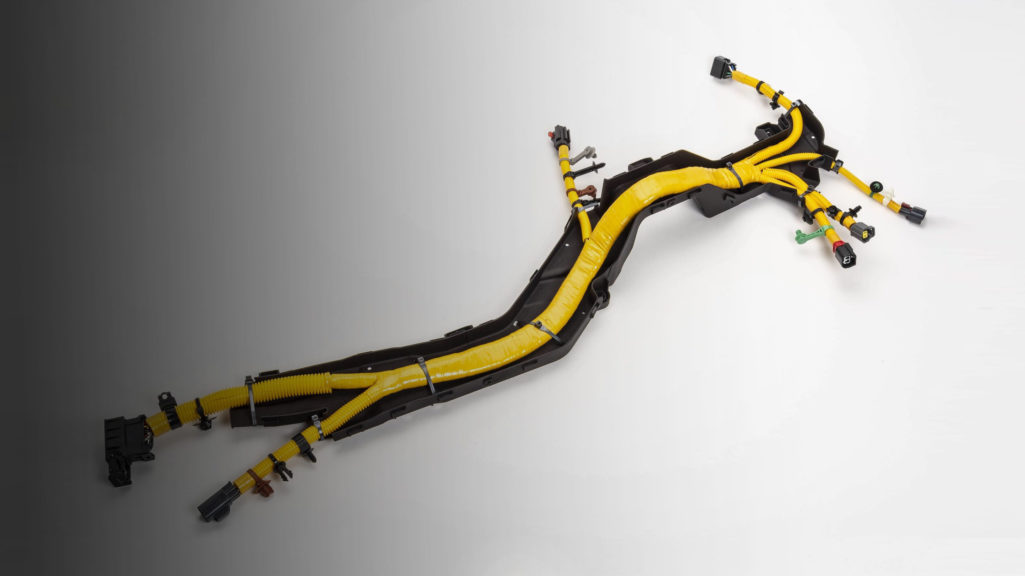
HellermannTyton needed to manufacture a package of wire routing aids for a prototype vehicle. These parts were large and complex, even for additive manufacturing, and the company was faced with a restricted timeline to meet customer demand. Fast Radius rose to the challenge and helped HellermannTyton produce plastic parts quickly.
THE CHALLENGE
Meeting tier one automotive expectations
HellermannTyton is a leader in designing and manufacturing cable management products. When automotive OEMs want innovative wire harness solutions, they turn to HellermannTyton. When the company came up against a project that required additive manufacturing and fast timelines, they turned to Fast Radius.
HellermannTyton was tasked by a tier one automotive company with manufacturing a series of wire routing aids for a new prototype vehicle. The plastic wire routing aids help mount and guide the wire harnesses throughout the vehicle’s interior, ensuring that electrical wires are safely secured. Due to the large size and complexity of these parts, HellermannTyton needed to modify the designs by splitting them into two to four smaller sections that could be produced within the machine’s build volume. The sections themselves aren’t small; each one could measure nearly 13 inches with the final assembly coming out at nearly 46 inches.
Typically, large plastic parts are a perfect fit for production injection molding. But this was a low-volume run, which meant that injection molding would be too costly. Not to mention, the team had exactly six weeks to produce over 1000 parts for the first run. HellermannTyton teamed up with Fast Radius to tap into their additive manufacturing capabilities needed and to meet the rigorous demands of the project.
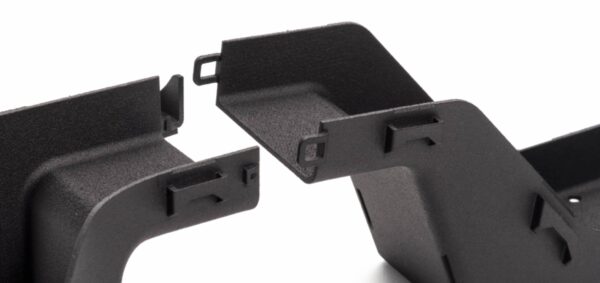
We like working with Fast Radius because they truly understand the needs of automotive companies. When it comes to this industry, Fast Radius knows what best-in-class looks like and how to deliver the parts we expect.

MAKING IT POSSIBLE
Powerful production capacity and expertise
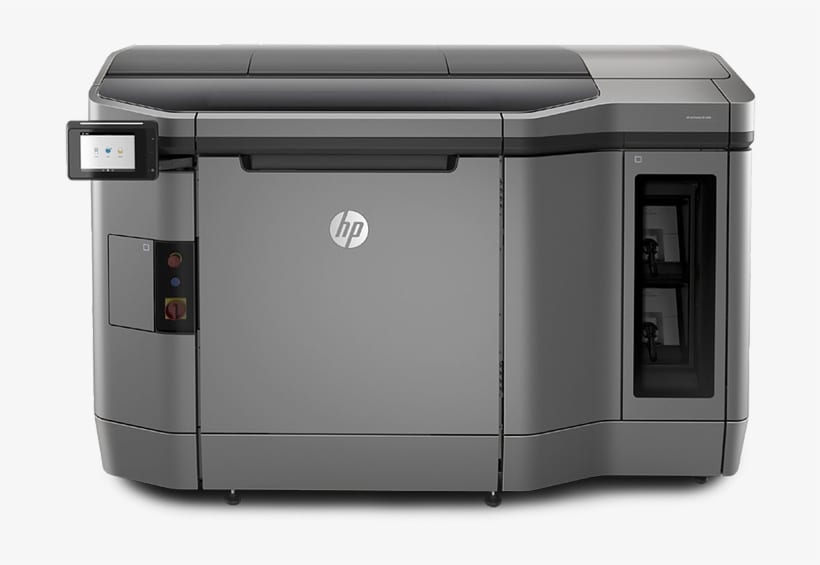
1. HP Multi Jet Fusion (MJF) capabilities
The combination of fast lead times, low-volume runs, and complex assemblage made additive manufacturing the right choice for production. However, it was important that the technology used to manufacture the routing aids had the right build capacity and materials to meet quality requirements. Because of these considerations, HellermannTyton chose HP MJF and PA12 for the project. Fast Radius had the production capacity through both their own fleet of HP MJF machines and their network of partners to meet the project’s lightning-fast timelines. This saved HellermannTyton time and costs by using Fast Radius as a one-stop shop for all of their MJF needs.
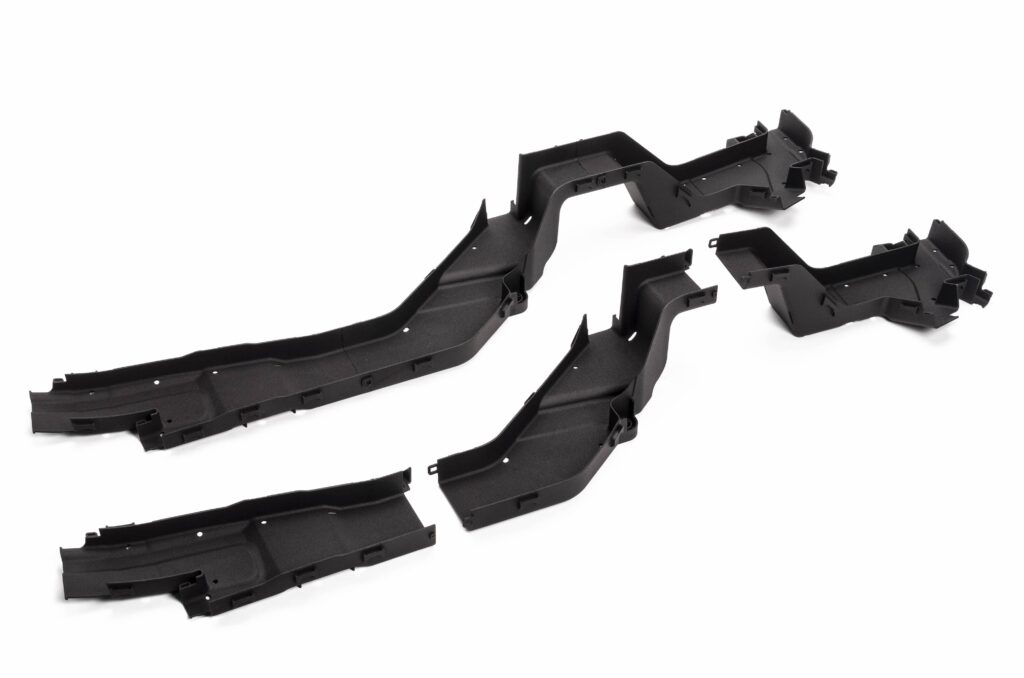
2. Simplified post-production and assembly
Each routing aid is custom-built to match the internal framework of the vehicle. The components have complex geometries that require assembly to the wiring harness. HellermannTyton worked with Fast Radius to print sections with mating geometry that when used in combination with adhesive creates a reliable finished product. Fast Radius’ on-site factory tech team worked closely with HellermannTyton to deliver on the post-processing requirements, which included part dyeing, assembly, and specialized shipping. The parts also had a very high success rate thanks to Fast Radius’ extensive experience in manufacturing with HP MJF.
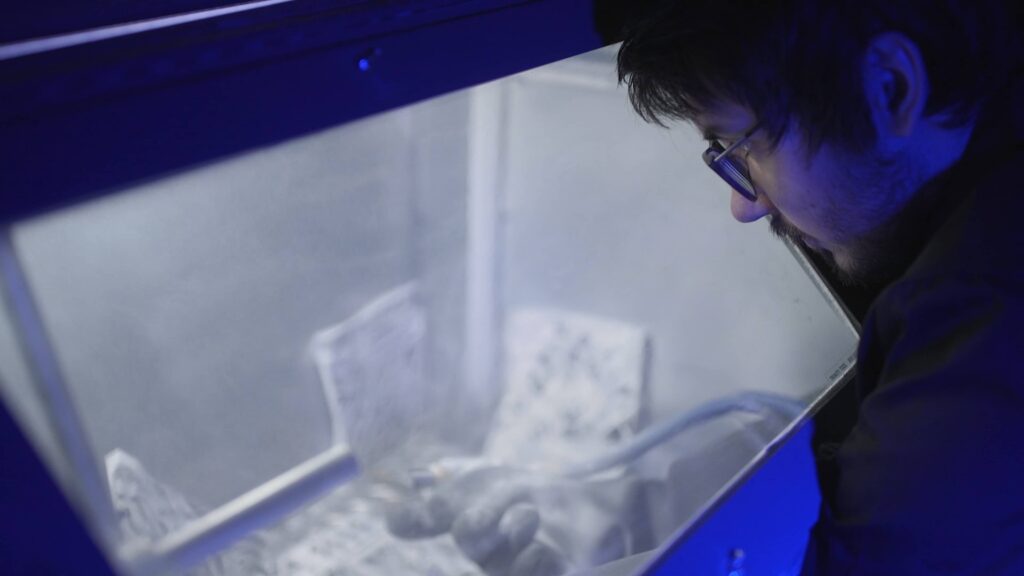
3. Agile and fast partnership
As the automotive industry continues to evolve and innovate, fast project timelines are becoming the norm. Fast Radius had six weeks to deliver the first few thousand parts. While some manufacturing partners would balk at that timeline, Fast Radius got right to work, ensuring the parts would be delivered on time at a very affordable cost. Fast Radius prides itself on being a true partner, flexible and quick so HellermannTyton could produce a big win with their customer.
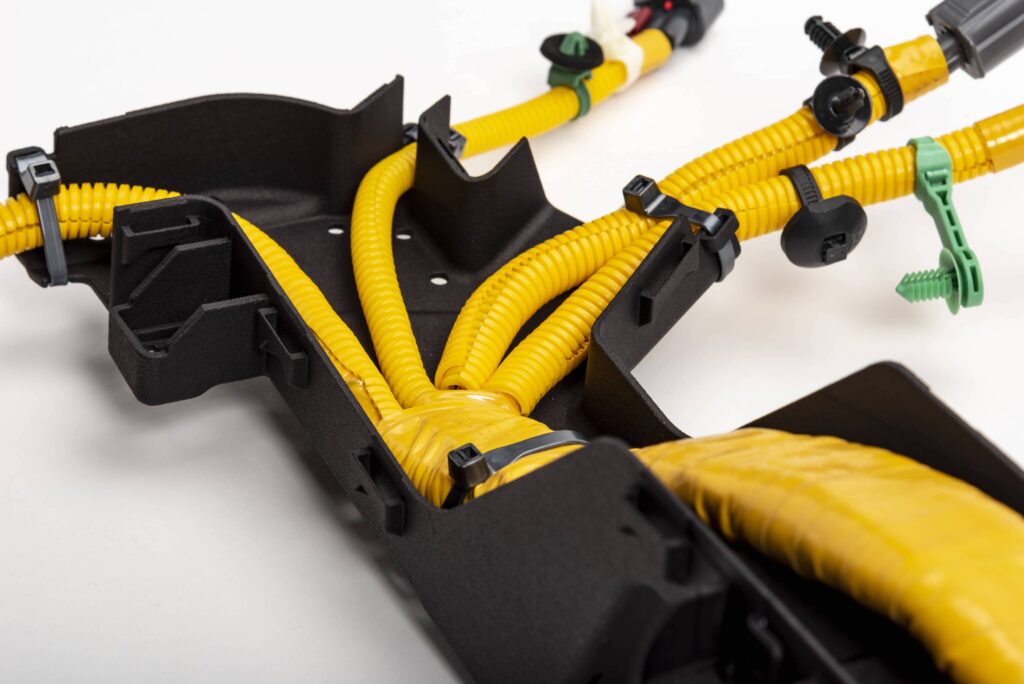
4. Reduced costs and lead times
HellermannTyton was able to eliminate the upfront cost of injection molding tooling and trials for the customer. It’s estimated that 3D printing saved nearly $1 million. Partnering with Fast Radius for additive manufacturing enabled HellermannTyton to meet the very fast lead time their customer required; the teams were able to save nearly two months in typical project lead time.
Gallery
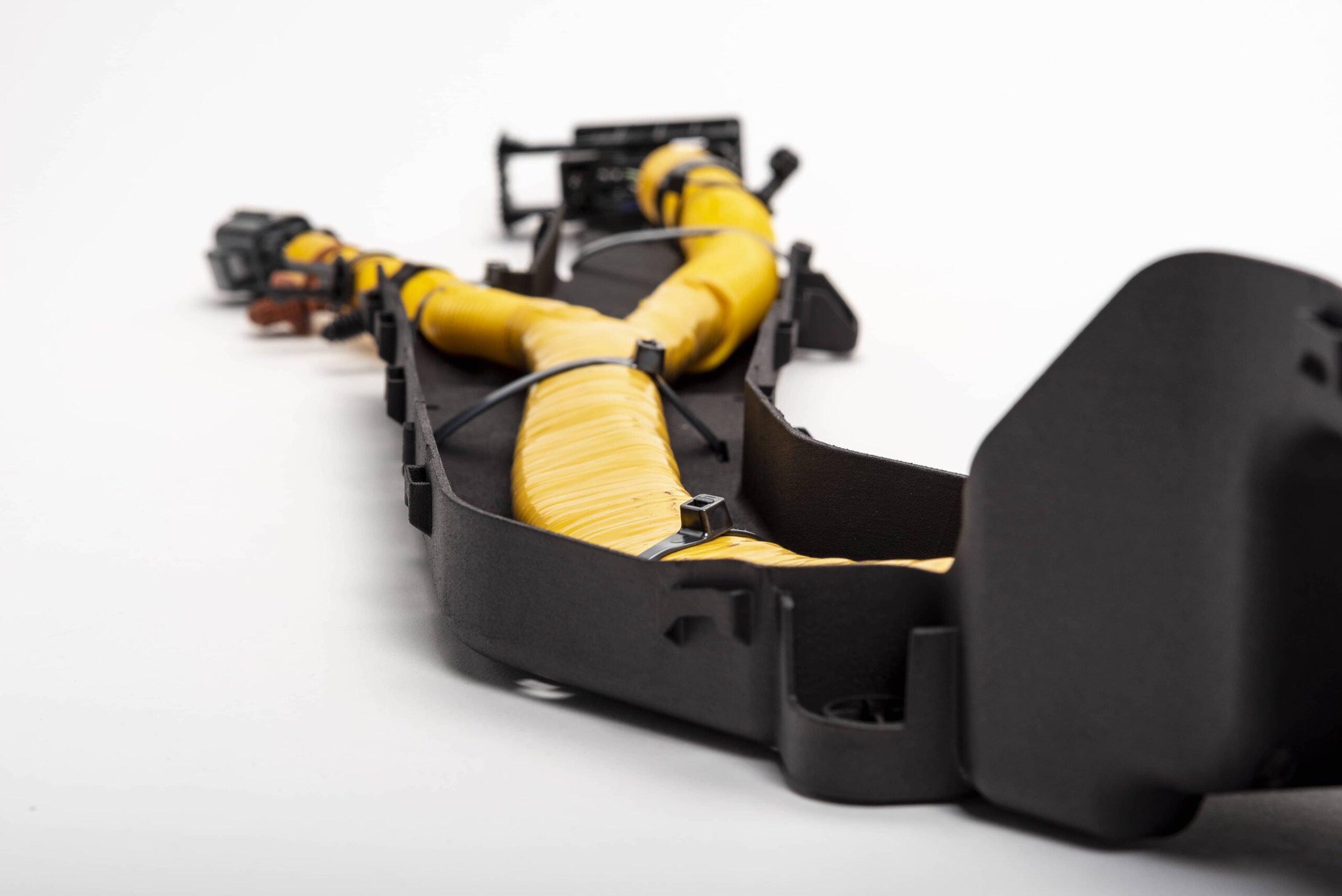
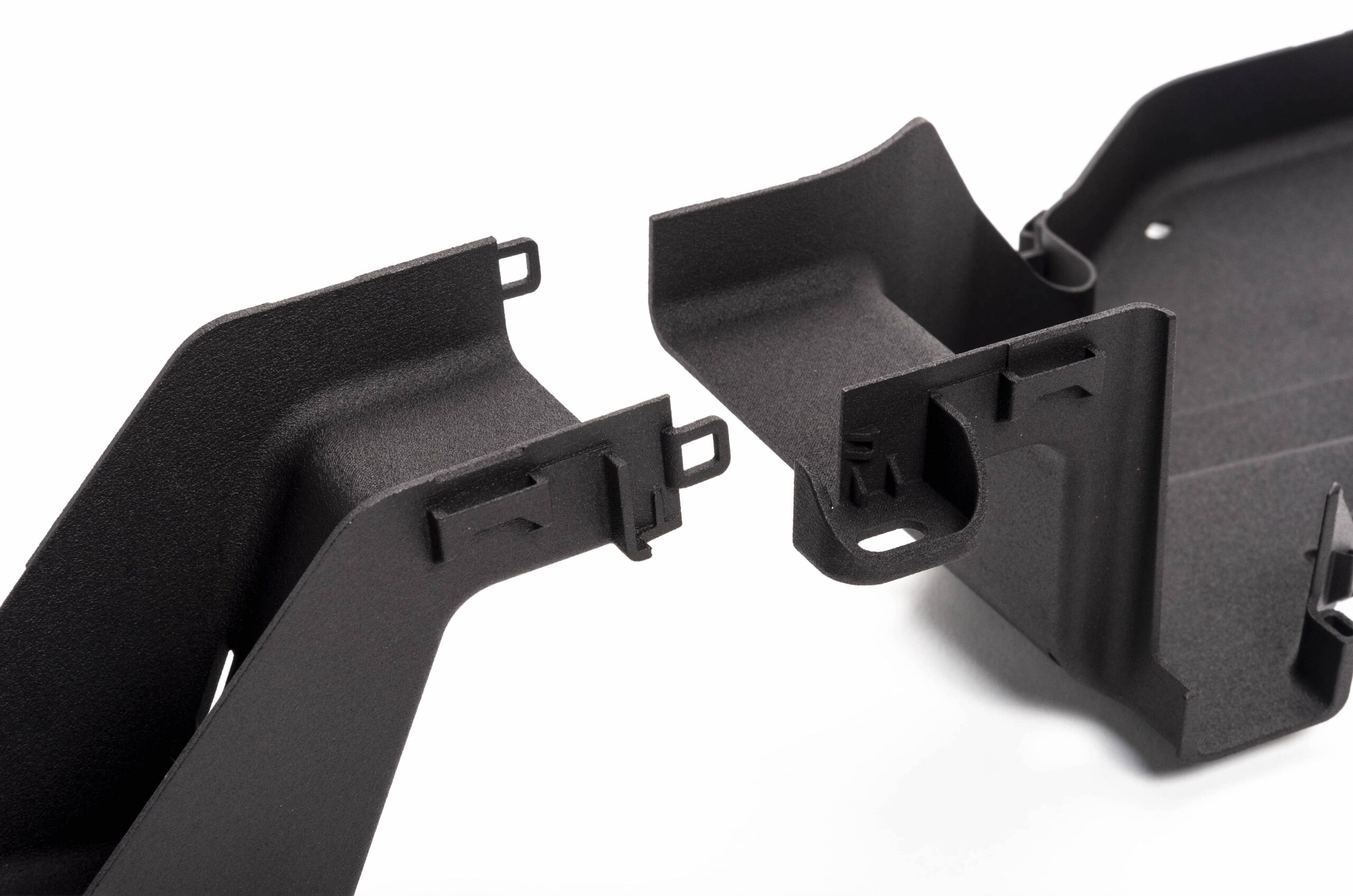
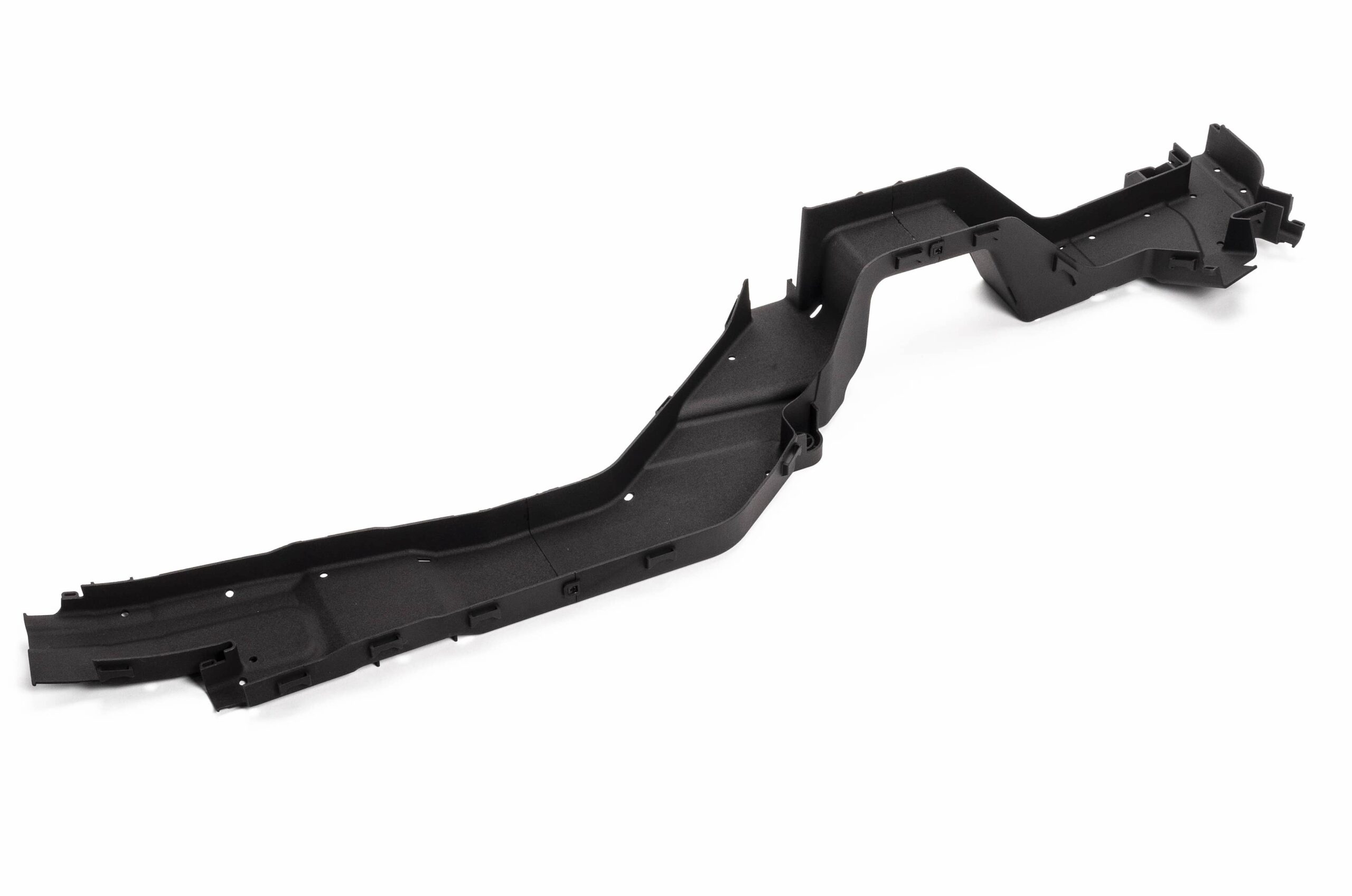
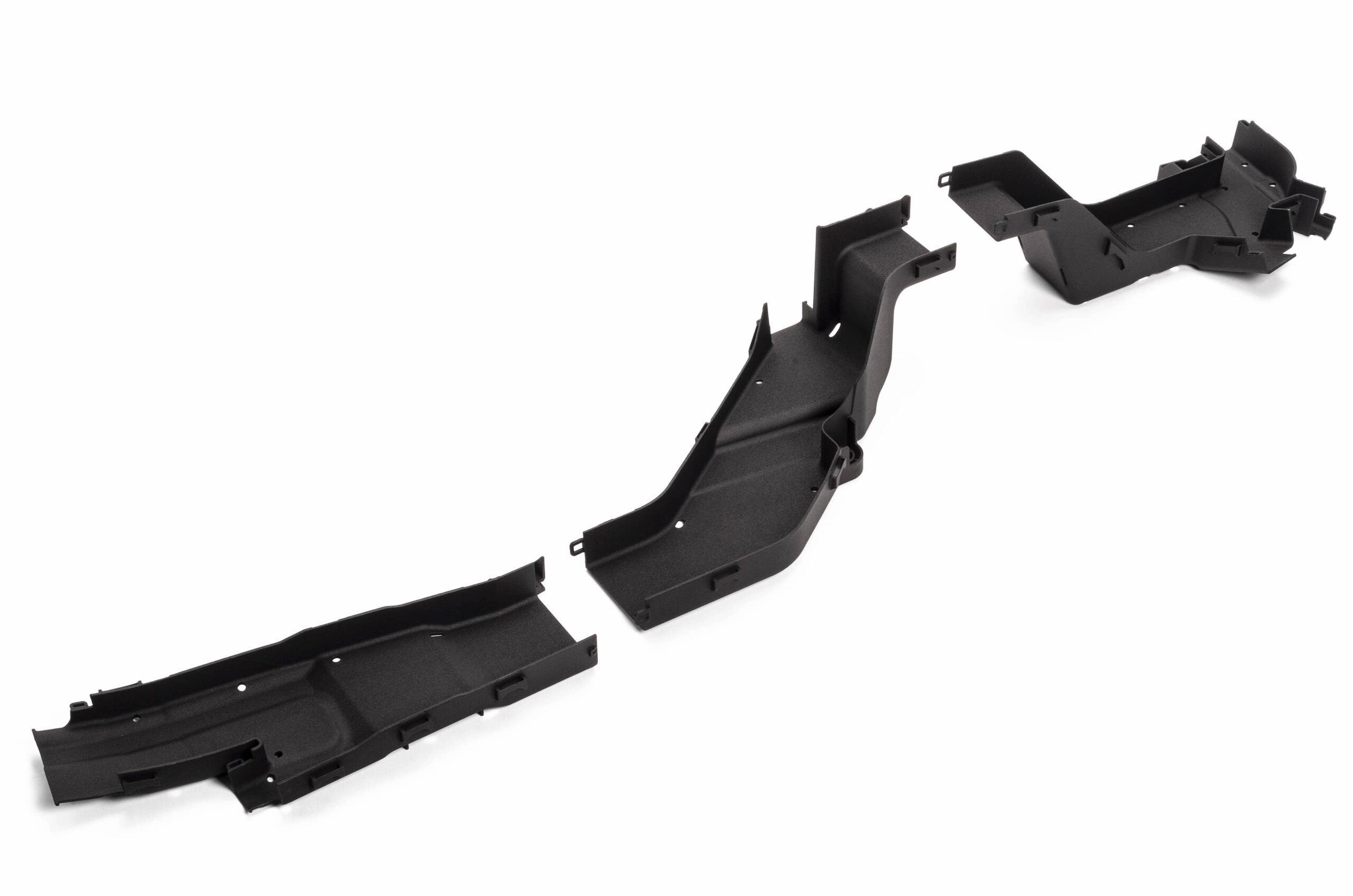
THE RESULTS
Additive manufacturing with Fast Radius saved HellermannTyton time and money
8 weeks
saved in lead time
$950K
saved in project costs
1,235 parts
assembled from 3,055 sections in 6 weeks